PTA Welding
Questions?
Our team is always here to assist with your Queries
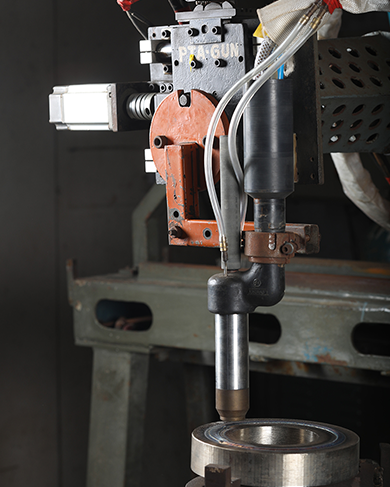
PTA Welding
Plasma Transferred Arc Process (PTA Process) is used to fuse a metallic coating to a substrate in order to improve its resistance against wear and/or corrosion.
During the process, metal powder is fed into a molten weld puddle (fusion bath) generated by the plasma arc at high temperature (up to 20,000 °C). All welding parameters, including powder feed, power input, plasma gas and shielding gas, as well as torch and work piece movement are automated and computer controlled.
PTA hard facing is a true welding process, with a metallic bond between the substrate and deposit. Deposit thickness can range from 0.6 to 6.0 mm, width from 3 to 10 mm when using a single pass; multi pass welding reaches deposit thickness up 20 mm and width over 30 mm.
The core of PTA process is PLASMA. The plasma (a gas sufficiently ionized to be electrically conductive) can be viewed as the natural state of matter (the so called fourth state of matter), with the other states existing only as variants to the normal.
In PTA hard facing, two DC power supplies are used to first establish a non-transferred arc (pilot arc ) between the tungsten electrode (-) and the anodic nozzle (+) and then a transferred arc between the tungsten electrode (-) and the work piece (+). The pilot arc is struck by a High Frequency device and the plasma gas flowing around the cathode is ionized at the electrode tip. When the transferred arc is ignited, the work piece becomes part of the electrical circuit and the plasma arc is directed and focused through the torch orifice into the work piece. Powder is metered, under a positive pressure of Argon flow, from the bottom of the torch into a pool of molten metal on the work piece surface.
The torch is then either moved by a side-beam carriage over the work piece, or the work piece is rotated or moved under the torch to produce a weld overlay deposit.
The plasma arc deposit is fully dense and metallurgic ally bonded to the work piece. The deposit microstructure is dense, with formation of dendrites during solidification. One of the most important features of the PTA process is the control of dilution. PTA produces dilution as low as 5%, compared to 20-25% typically obtained when hard facing by MGAW (MIG) and GTAW (TIG) processes. So it is possible to maintain the noble properties of deposit even in one single pass.