Valve
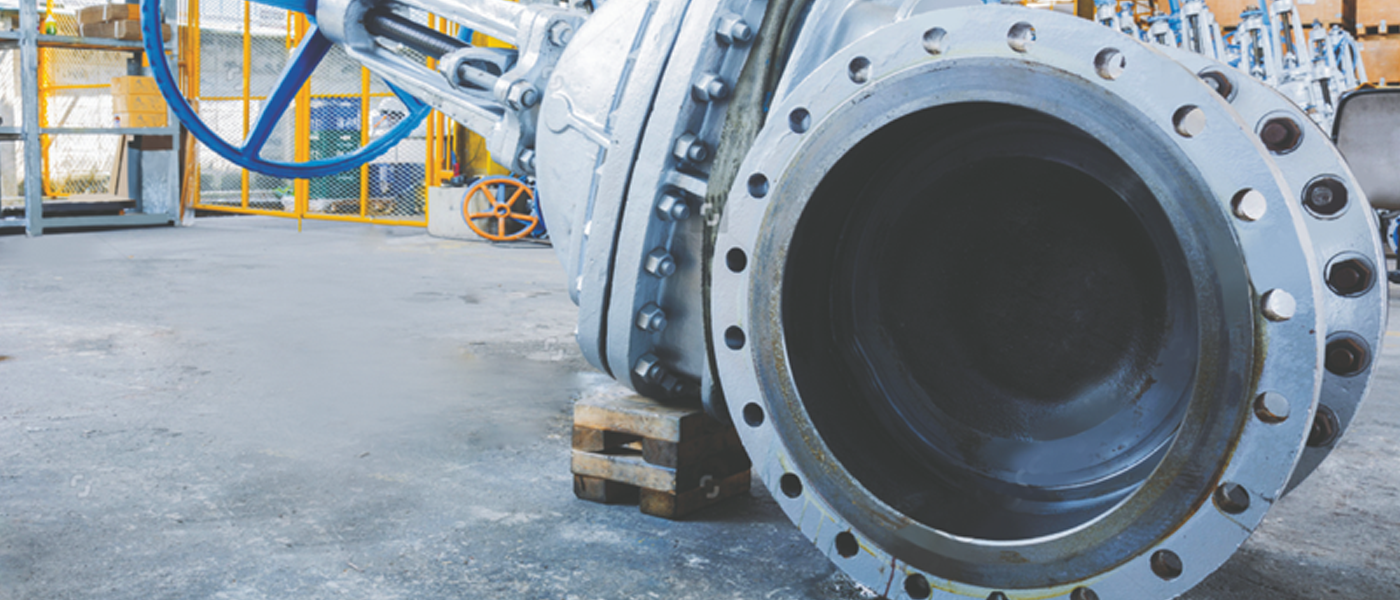
Pumps and Ball Valve Overview
Pumps and Valves are a significant part in transfer of media such as chemicals, fluids, resins, gases etc. specifically in the Oil & Gas and Chemical industries where the nature of media is extremely abrasive and corrosive. Pump components are subject to abrasion, erosion, cavitation and sliding wear during process. Abrasion and erosion results from abrasive particles in the medium being pumped, but even in the absence of any abrasive particles, sliding wear can occur due to unintentional contact between rotating and stationery components. Moreover these wear rates in pumps are often unexpectedly high because of the synergistic relationship between wear and corrosion. As the pump components in the flow path wear, clearance between sealing surfaces increase and vane angles change, resulting in increased vibration or leakage and decrease in pump efficiency over time. A range of Thermal spray coatings for different components in the pump and valve assembly exhibit improved wear and corrosion resistance thereby increasing the operational life and reducing downtime costs.
A ball valve is a device which controls flow of fluids and gases through it by its rotary motion along an axis. The bore at the center of the ball allows the media to pass when it is aligned with the direction of pipeline.
Gate valve serves the same purpose as that of ball valve. However it’s a rectangular piece of solid with through bore towards one end. The gate moves linearly along an axis when the valve is rotated. Knife gate valve has a similar mechanism with thinner cross section and tapered edge on one end.
These valves are secured in position with the help of metal seats such that it provides proper sealing when it’s in off position. However in certain critical applications where the media passing through the valves are abrasive, erosive or corrosive in nature such as slurries, mud, salt water, Hydrogen sulphide, Hydrochloric acid, high temperature fluids and gases etc., the surface of ball/gate and seat tends to wear out due to repeated action of the valve. As a result the sealing of the valve gets compromised thereby causing leakage and uncontrolled flow of media. In applications where the flow control mechanism is at most critical for the process it may lead to sub-standard quality of the process output or even hazards.
Wear and Corrosion Resistant Coatings
We offer a variety of Thermal spray coatings and claddings that increase the operational life and performance of ball valves and gate valves. Our range of tungsten carbide coatings is engineered to sustain extreme abrasive, erosive and corrosive operating conditions. Our coating material selection is based on nature of media being handled, temperature, type of wear and compatibility with base material. The coatings are applied with robotic controlled HP-HVOF process that produces a dense and homogeneous coating with very strong mechanical adhesion to the base material. We can also provide weld overlays of stellite, Inconel and carbide based material deposited with our automated and controlled PTAW process. The coatings are ground and lapped, further reducing the co-efficient of friction and enhancing the sliding properties to reduce wear of mating seal parts. Our wear and corrosion resistant coatings will help you to increase productivity, reduce downtime and decrase maintenance costs.
Few critical applications where our coated valves are being used are listed below :
Industry | Application |
---|---|
Oil & Gas | Platform and subsea pipelines carrying petroleum products and by products |
Mining | Pipelines handling gold, silver and copper products |
Paper and Pulp | Valves handling slurries and steam from paper processing machines |
Steam | High and low pressure steam in turbine drain system |
Coating Properties | PIC C53 | PIC DC09 | PIC DC12 |
---|---|---|---|
Micro Hardness (HV0.3) | 380 - 500 | 1100 - 1400 | 800 - 1100 |
Coating Application | Erosion and Corrosion Resistance | Abrasion and Corrosion Resistance | High Temperature Corrosion Resistance |
Bond Strength | >10000 Psi | ||
Finish Coating Thickness | 200 to 300 µm | ||
Surface Finish | < 0.4 Ra µm |