Thermal Power
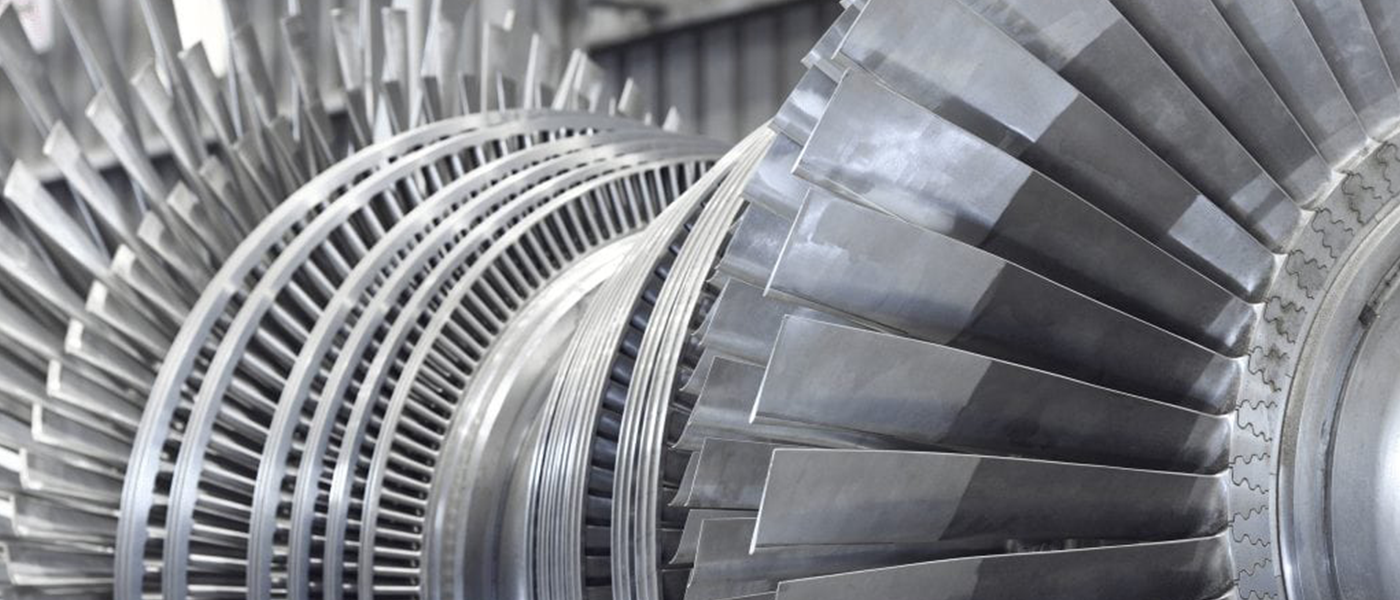
Thermal Power
Steam Turbine Components
A steam turbine is a device that extracts thermal energy from super-heated high velocity pressurized steam and uses it to do mechanical work on a rotating output shaft. In the process blade tips of LP turbine rotor get worn out due to droplet erosion thereby reducing the efficiency of rotor. Also solids contained in dirty steam cause wear on critical components such as rotor and stator blades, sealing areas and other zones subjected to the steam flow. Also the bearing journals of rotors are subjected to sliding wear due to rotation at high RPM. The entire steam turbine system consist of a series of valve component assemblies of which many areas are subjected to severe abrasive, corrosive and erosive wear. Premature failure of any of these components will not only lead to heavy downtime and maintenance costs but also prove to be fatal.
Boiler Tubes
Boiler tube coating consists of a series of tubes that contain high pressure flowing water which is heated externally by fire. Boiler tubes are subjected to temperatures which make them more vulnerable to erosion from abrasive soot emitted from burning of coal. Continuous bombardment leads to reduction in wall thickness that eventually leads to failure
Steam Turbine Components - High Temperature Wear, Erosion and Corrosion Resistant Coatings
- HP Turbine Blades for erosion resistance
- LP Turbine Blades to combat droplet erosion
- Steam Control Valve componen
- Abradable coatings for Turbine Casings for better clearance control & prevent steam leakage
- Insulating washers for thermal and electrical insulation
- Babbitt coating for bearing bush
- Diffusers
- Valve Spindle with Cone
- Valve Cone
- Valve Cone Extension
- Valve Seats
- Guide Bush
- Angle Rings
- Contour Rings
- Insulating Washers etc.
Coating Properties | PIC C52 | PIC C53 | PIC DC07 | PIC DC12 |
---|---|---|---|---|
Process | GTAW/PTAW | GTAW/PTAW | HVOF | HVOF |
Bonding | Metallurgical | Metallurgical | Mechanical | Mechanical |
Micro Hardness (HRc) | 28 - 36 | 42 - 48 | 72 - 74 | 68 - 72 |
Coating Application | High Temperature Oxidation and Impact Resistance | Erosion and Corrosion Resistance | Erosion and Corrosion Resistance | High Temperature Abrasion and Corrosion Resistance |
Max Temperature (°C) | < 600 | < 600 | < 700 | < 850 |
Surface Finish | < 1.6 Ra µm | < 1.6 Ra µm | < 0.8 Ra µm | < 0.8 Ra µm |
Wear and Corrosion Resistant Coatings on Rotor Bearing Journals
Coating Properties | PIC DC09 | PIC B02 |
---|---|---|
Process | HVOF | Plasma |
Bonding | Mechanical | Mechanical |
Micro Hardness (HRc) | 72 - 74 | 68 - 72 |
Coating Application | Abrasion and Sliding Wear Resistance | Abrasion and Corrosion Resistance |
Max Temperature (°C) | < 450 | < 540 |
Surface Finish | < 0.4 Ra µm |