System Capabilities
Next-Level Functionality With World Class Manufacturing Practices
We keep ourself updated with the latest Manufacturing Techniques and Quality Standards which sets us apart from our Competition. These practices embedded in our culture has encouraged us to transform at a rapid pace whilst also providing an enriching experience to our clients.
6S
Our Departments are grouped in to Cross Functional Teams with assigned roles and responsibilities of 6S activities. All employees are trained about the 6S methodology and teams are mandated to spend 15 minutes every day for 6S activities. This has created a great degree of awareness on Product Safety and Standardization which in return provides value to the Customer.
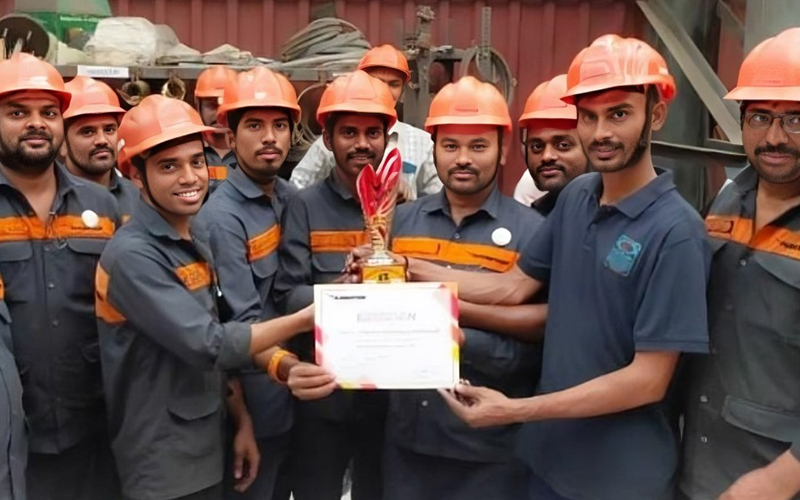

KAIZEN
At PLASMATRON, Continual Improvement is a way of life and this intent is reinforced by the Top Management by establishing a procedure for the same and being a part of its Executing Committee. Our stakeholders at the lowest level of hierarchy are encouraged to put up their valuable suggestions which are reviewed and implemented with support of Management Team. KAIZEN’s are categorized in to PQCDSM based on its benefits which becomes an intangible deliverable to the Customer.
ERP
A customized Business Management System incorporating interlinked modules covering right from Lead Generation to Accounting and Customer Feedback. Customer component is identified immediately after GRN and its production life cycle can be tracked through the ERP system. The ERP is equipped with high data handling capacity and access controls to ensure long term preservation and security of customer documents.
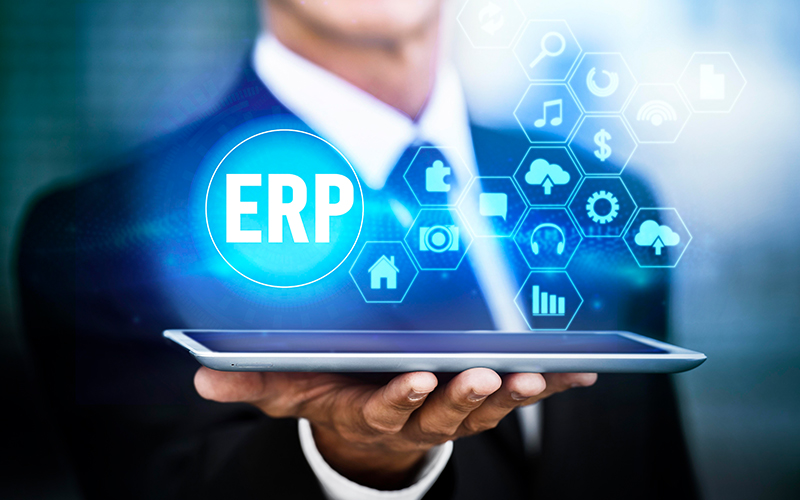
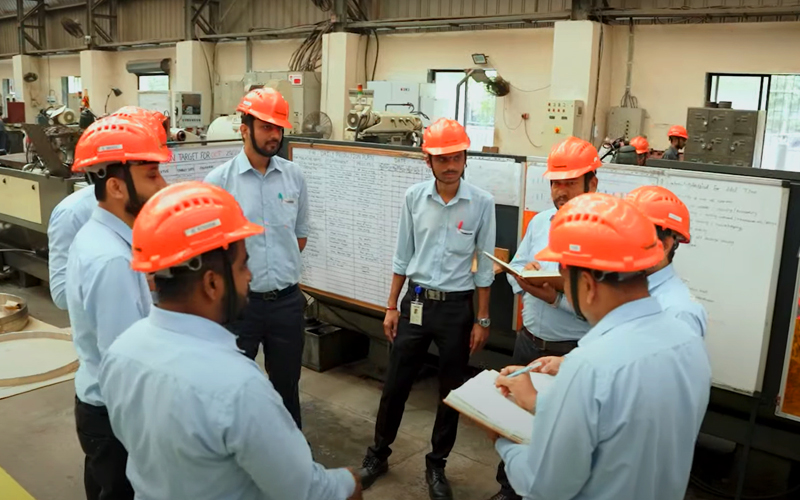
Production Scheduler
An integrated production scheduling system which provides live update of each component. Plan vs Actual activities are tracked on a daily basis and corrective actions taken accordingly. Customers are given realistic commitments based on data available through this scheduler.
OEE
Details of each process is documented in a format broadly capturing the Machine Utilization, Operator Efficiency and Product Quality. These details are compiled and evaluated each day to calculate the OEE and corrective actions are taken accordingly. This monitoring mechanism has enabled us to improvise every day and provide good quality products to our Customers on Time.


RCCA
We follow a documented Root Cause and Corrective Action procedure integrated in our ERP system, which is in accordance with Root Cause Analysis and Problem Solving – Section 7.4, published on the IAQG portal. The step by step Root Cause Analysis and Corrective Action implementation process has inculcated problem solving attitude in each of our employees.
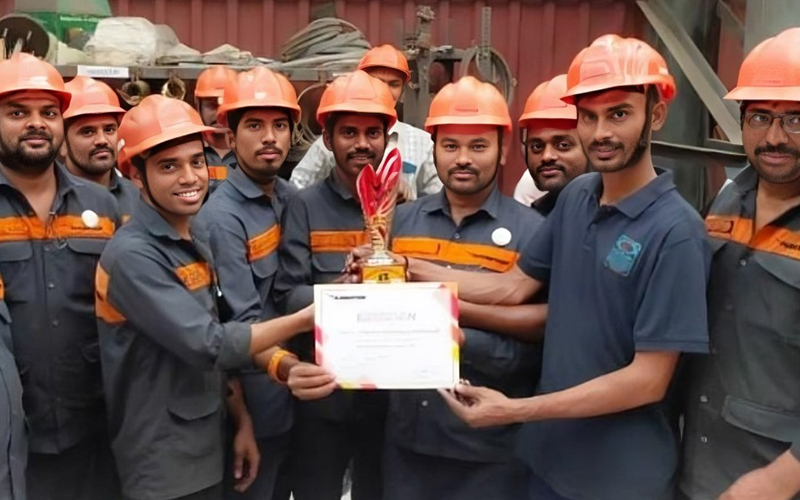
6S
Our Departments are grouped in to Cross Functional Teams with assigned roles and responsibilities of 6S activities. All employees are trained about the 6S methodology and teams are mandated to spend 15 minutes every day for 6S activities. This has created a great degree of awareness on Product Safety and Standardization which in return provides value to the Customer.
KAIZEN
At PLASMATRON, Continual Improvement is a way of life and this intent is reinforced by the Top Management by establishing a procedure for the same and being a part of its Executing Committee. Our stakeholders at the lowest level of hierarchy are encouraged to put up their valuable suggestions which are reviewed and implemented with support of Management Team. KAIZEN’s are categorized in to PQCDSM based on its benefits which becomes an intangible deliverable to the Customer.

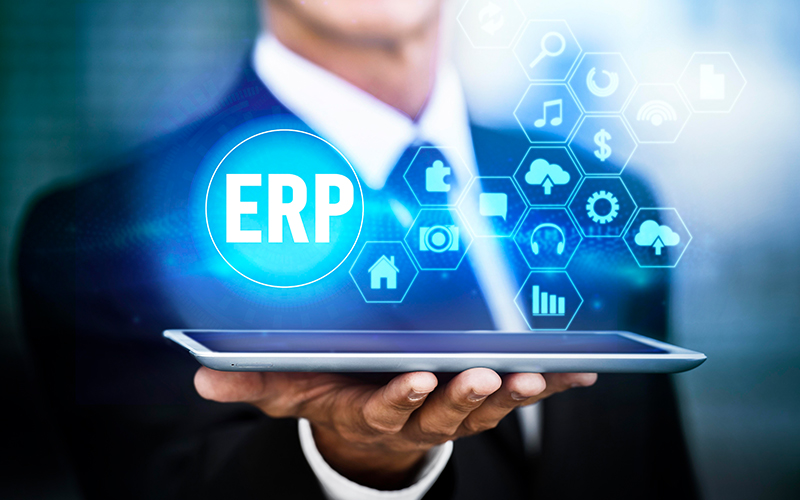
ERP
A customized Business Management System incorporating interlinked modules covering right from Lead Generation to Accounting and Customer Feedback. Customer component is identified immediately after GRN and its production life cycle can be tracked through the ERP system. The ERP is equipped with high data handling capacity and access controls to ensure long term preservation and security of customer documents.
Production Scheduler
An integrated production scheduling system which provides live update of each component. Plan vs Actual activities are tracked on a daily basis and corrective actions taken accordingly. Customers are given realistic commitments based on data available through this scheduler.
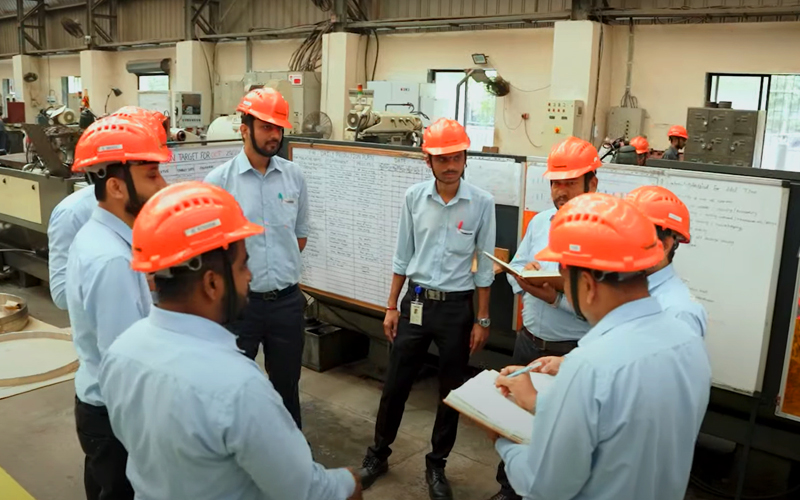

OEE
Details of each process is documented in a format broadly capturing the Machine Utilization, Operator Efficiency and Product Quality. These details are compiled and evaluated each day to calculate the OEE and corrective actions are taken accordingly. This monitoring mechanism has enabled us to improvise every day and provide good quality products to our Customers on Time.
RCCA
We follow a documented Root Cause and Corrective Action procedure integrated in our ERP system, which is in accordance with Root Cause Analysis and Problem Solving – Section 7.4, published on the IAQG portal. The step by step Root Cause Analysis and Corrective Action implementation process has inculcated problem solving attitude in each of our employees.
