Spray and Fuse
Questions?
Our team is always here to assist with your Queries
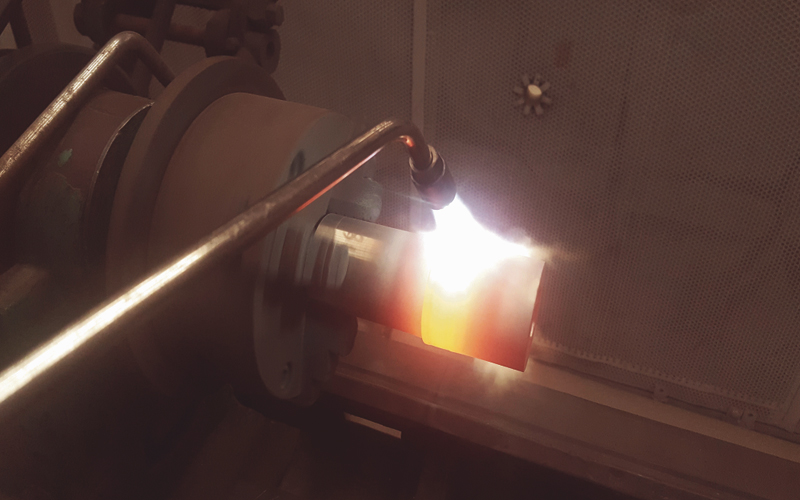
Spray and Fuse
Spray and Fuse is an extension of coatings done by Powder Flame Spray process wherein the sprayed coating is fused with the base material by application of external heat energy using Oxy-Acetylene torch, Induction coil, Furnace, Laser beam or an external heating source. As the process requires the application of heat to fuse the coating to the substrate, consideration shall be given to the possible effects of such heating on the substrate, including distortion, scaling, need to stress relieve and irreversible transformation of mechanical and/or metallurgical properties. Spray and Fuse can be carried out in two ways :
Spray with simultaneous Fusion
This is a manual process using an oxy/acetylene torch fitted with a hopper. A suitable self-fluxing powder is fed via the hopper into the gas stream, through the flame and on to the component where it is simultaneously fused. The continuous process of pre-heating the work-piece with the flame through which the powder is fed and fused produces a coating with properties dependent on the choice of self-fluxing powder.
Spray and subsequently Fuse
It is a manual or mechanized process using a powder flame spray gun to apply the required thickness of coating material to the component. This sprayed coating is subsequently fused. A selected self-fluxing alloy powder is fed via a powder hopper into the carrier gas, through the flame, on to the work-piece until the desired thickness is achieved. Fusing of the deposit is a separate operation performed as soon as possible after spraying.
In both the above methods, the coating is taken to solidus temperature (1020 to 1100°C). At this temperature coating fuses and voids and porosity in the coating collapses making the coating more dense and homogeneous. This also forms a fine metallurgical bond with the prepared substrate which makes the coating capable of enduring impacts. The rate and duration of heating and the temperature range is critical and will vary according to the composition of the coating alloy and the size and complexity of the component. A very good indication of proper fusing is the appearance of the coating. Once properly fused, the coating will have a reflective orange surface or a “glaze”. At this point the reflection of the gun/flame can also be seen on the coating surface.
A variety of materials can be deposited by this process to achieve properties required for different critical applications such as :
- Cobalt based material
- Nickel based material
- Carbide based variants etc.