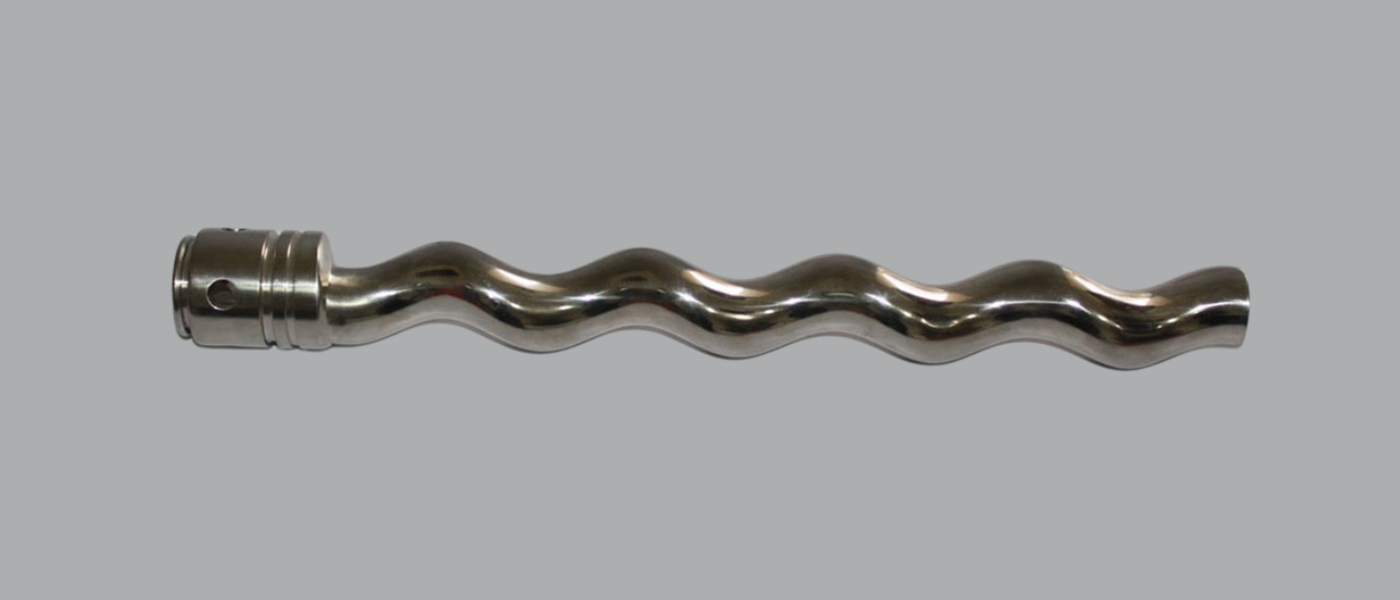
Progressive Cavity Pump
Problem
A progressive cavity pump is a type of positive displacement pump used for transferring fluids by rotation of rotor. The rotor seal tightly against the stator as it rotates, forming a set of fixed-size cavities in between. The pumped material moves inside these cavities when the rotor rotates. Applications which involve flow of slurries and other abrasive and corrosive substance can lead to severe damage to rotor over a period of time. This will eventually wear out the stator thereby increasing the clearance and decreasing the pumping efficiency. Prolonged operation will lead to unexpected breakdown and heavy maintenance costs.
Solution
PIC DC Range of Coatings
Our tungsten carbide based coatings provide excellent abrasion and corrosion resistance against harsh fluids flowing through progressive pumps. Our range of coatings can be applied with HP-HVOF process that produces a dense and homogeneous coating through repeated and controlled deposition. The coatings are ground and super finished with at most precision to achieve desired size and surface finish. Post-coating finish plays a vital role in the operational life and performance of rotors. A smooth finish of rotor will promote flow ability and prevent adherence of abrasive and corrosive particles on the surface. Our range of coating solutions proves to be the best replacement for hard chrome plated and nitrided rotors and improves the operational life by 5 – 8x. We have complete in-house setup for coating and super finishing of rotors.
Coating Properties | PIC DC09 | PIC DC12 |
---|---|---|
Micro Hardness (HV0.3) | 1100 - 1400 | 800 - 1100 |
Coating Application | Abrasion and Corrosion Resistance | High Temperature Corrosion Resistance |
Max Temperature (°C) | < 450 | < 850 |
Bond Strength | >10000 Psi | |
Finish Coating Thickness | 150 to 200 µm | |
Surface Finish | < 0.8 Ra µm |