Hydro Power
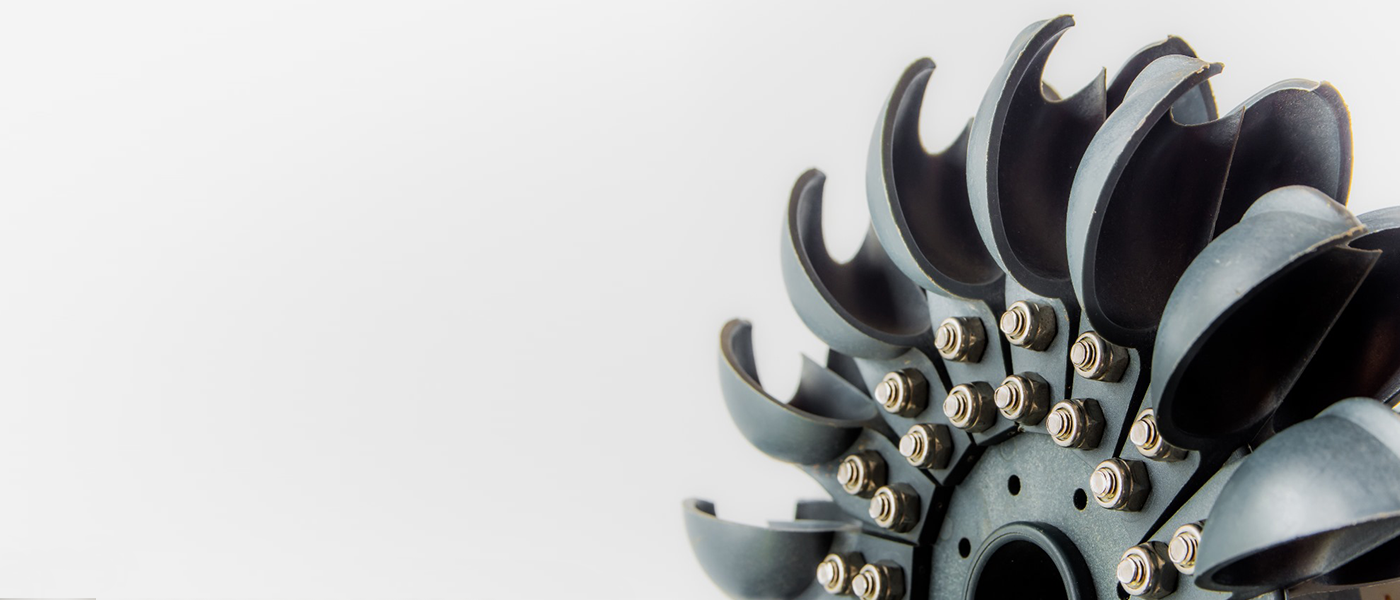
Hydro Power
Problem
Hydropower refers to conversion of energy from flowing water into electricity. It is one of the most environmental friendly renewable energy sources with absolutely no carbon or harmful emissions in contrast to burning of fossil fuels in Thermal power stations.
The Hydro turbine is the heart of the power station. Different Hydro turbines such as Pelton, Francis and Kaplan are subjected to high flow rates of water which often contain abrasive sediments and quartz. Constant bombarding of these abrasive particles on the buckets may lead to erosion of base material. This erosion not only leads to reduction in efficiency and operational life of the turbine but also affects day to day operation and maintenance cycles. Removal of turbine for maintenance activities in itself is very difficult, tedious, time consuming and involves lot of additional resources.
Cavitation is also a dominating factor in case of hydro turbines. Low pressure regions of high flow reaction turbines are subjected to heavy cavitation wear. Unplanned stoppages of hydro power plants could lead to heavy operational losses.
These hydro turbines are operated for decades due to which critical sub-assembly parts such as shafts and rings also get worn out. Replacement of these parts tends to be very expensive and time consuming. Other parts which get worn out include guide blades, retainer plates, cones etc.
Solution
HYDREX DC09
To increase reliability of these turbines, the components coming in contact with the high pressure water such as buckets, retainer plates, guide blades, cones, etc. are coated with high density and wear resistant HYDREX DC09 coatings that impart high erosion and cavitation endurance. These coatings are deposited with robotic controlled HP-HVOF process to get uniform coating deposition and further impregnated with special sealant to achieve dense coating. Coating properties of HYDREX DC09 is as stated below :
Coating Properties | HYDREX DC09 |
---|---|
Micro Hardness | 1100 - 1400 HV0.3 |
Porosity | < 0.8% |
Bond Strength | > 10000 Psi |
Abrasion Resistance | Excellent |
Corrosion Resistance | Very Good |
Max Temperature | < 450°C |
WC ALLOYS
Dimensional restoration of parts such as shafts and rings can be done through Twin Wire Arc Spray process by depositing a range of our WC Alloy materials. To achieve higher wear resistance and optimal coating properties, the base coat is followed by a top coat of superior coating material such as alloy or carbide deposited through Plasma or HP-HVOF process. These coatings are ground to achieve the desired dimensions and tolerances