Plastic
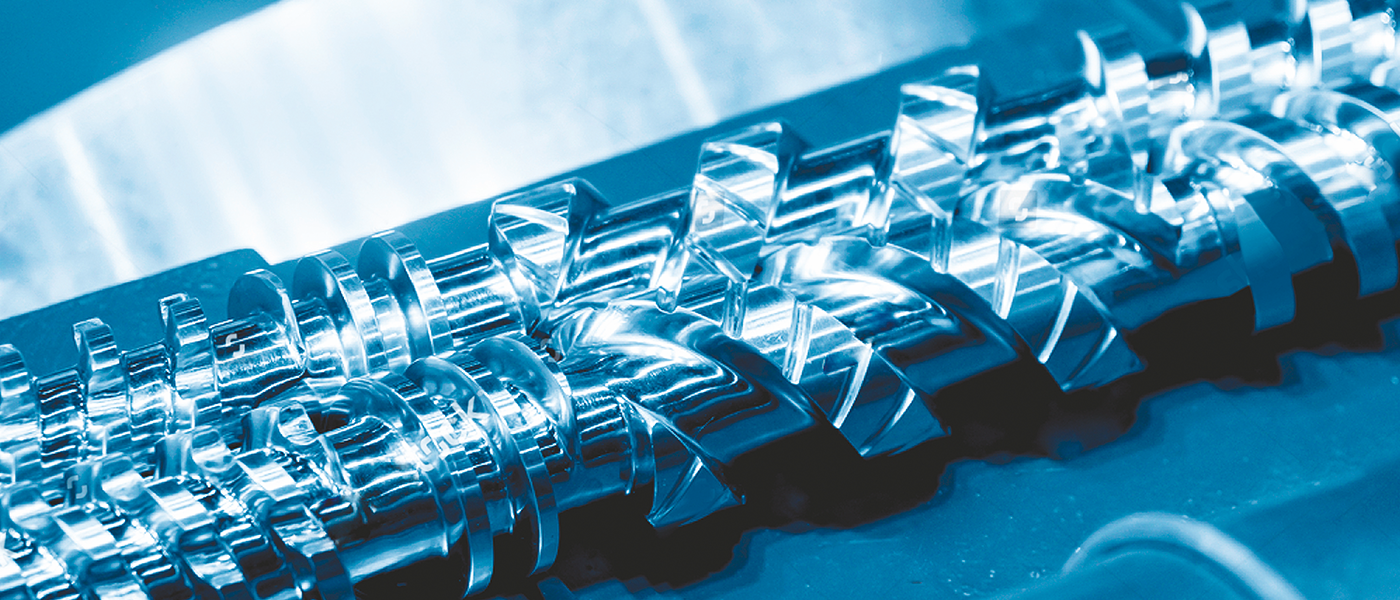
Overview
Plastic Extrusion is a widely commercial process in which raw thermoplastic material is converted into a finished plastic product through a continuous extrusion process. Certain additives are introduced in the process to impart specific mechanical properties to the product. The entire extrusion cycle is completed after the raw material passes through three extreme operating environments. The abrasive and corrosive nature of the raw material coupled with the harsh operating conditions makes it inevitable for the screw and barrel to deteriorate over time thereby increasing the functional clearance between the two. This in turn leads to low productivity and intermittent defects in the end product which if ignored over a period eventually causes the operation to cease. Thermal sprayed tungsten carbide variants and cermet based coatings enhance the wear and corrosion resistant properties of the screw thereby increasing its operational life and reducing productivity and downtime loss.
TRIBODEX™ Range of Cermet Coatings for Feed Screws
Problem
Solution
TRIBODEX™ DC Range of Coatings
We offer advanced cermet based coatings that endure high abrasion and corrosion as encountered during plastic extrusion process. Coatings prolong operational life of feeder screws without deteriorating performance. In comparison to Hard Chrome plating, Tribodex DC coatings impart 6 – 10x higher operational life.
Finely distributed carbides in metal matrix are deposited on extrusion screw through HP-HVOF process to achieve homogeneity, high hardness and excellent adhesion meant to combat the harshest operating conditions. Our automated and optimized process ensures minimum dilution of carbide crystals which results in coatings with higher strain endurance. Post coating finishing is the most critical part of Tribodex DC coated screws. After coating, the screws are ground and polished to the required dimensions and profile as specified by customer. We have specialized measuring and monitoring instruments dedicated for inspection of screws.
Based on the application and type and extent of wear, we provide two coating option :
- Full encapsulation
- Coating on flights
Coating Properties | DC07 | DC09 | DC09-SX |
---|---|---|---|
Micro Hardness (HRc) | 68 to 72 | 68 to 73 | 70 to 74 |
Abrasion Resistance | Very Good | Excellent | Excellent |
Corrosion Resistance | Very Good | Very Good | Very Good |
Bond Strength | >10000 Psi | ||
Finish Coating Thickness | 200 to 275 µm | ||
Surface Finish | < 0.4 Ra µm |