Housings
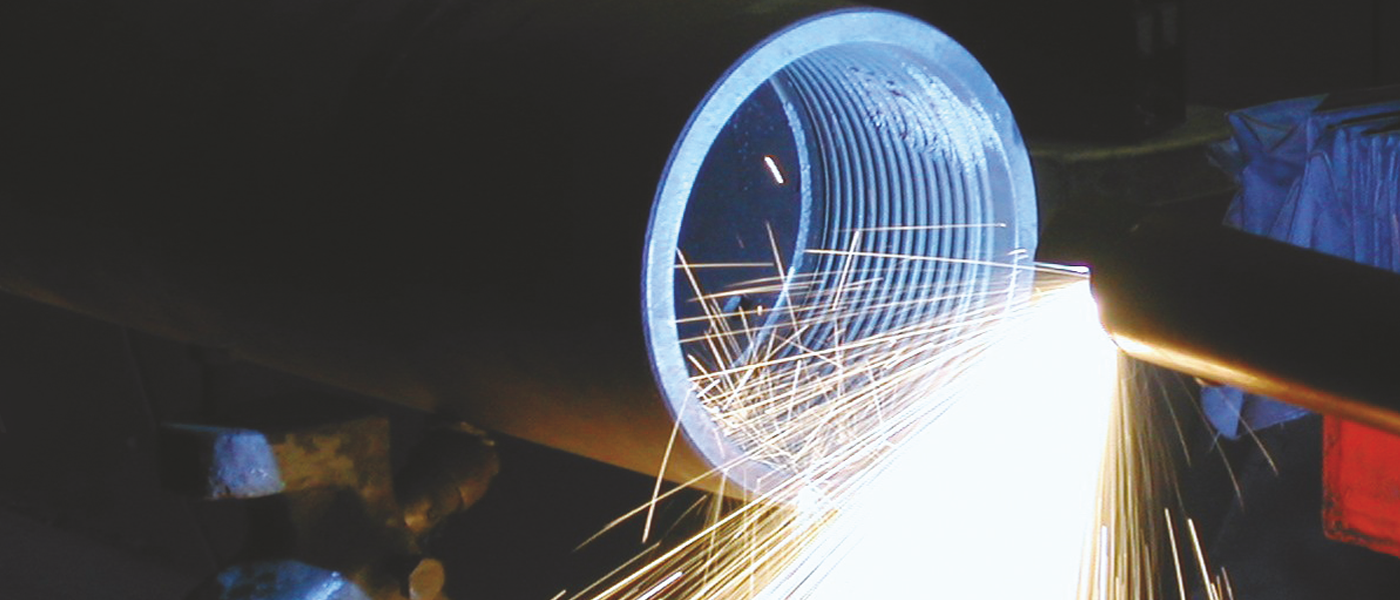
Housings
Problem
Solution
PIC WC200 Series Coating
Our WC200 range of coatings is deposited in the inside diameter of Housings through Twin Wire Arc spray process. These coatings provide good wear and corrosion resistance against slurries during pumping action. The base metal is prepared by machining threads on the coating surface to facilitate better bonding. After coating the surface is machined to achieve pre-honing dimensions. Final size and surface finish is achieved by Honing. We have in-house capabilities for coatings on new parts as well as complete repair and refurbishment on worn out parts. Worn out housings cannot be repaired with hard chrome plating beyond a certain limit due to coating thickness constraints. Our PIC WC200 range of coatings can overcome this limitation and provide optimal life.
We have also indigenously developed Inconel 625 weld overlays on new housing parts. Our PIC WC25 coated housings can sustain extreme abrasive and corrosive applications and have been successfully tested in operation. The metallurgic ally bonded coating also provides resistance to impact and abnormal vibrations. The overlay is machined and honed to required size and surface finish as per customer specifications.
Coating Properties | PIC WC200 Series | PIC WC25 |
---|---|---|
Process | Twin Wire Arc Spray | GTAW |
Bonding | Mechanical | Metallurgical |
Micro Hardness | 300 – 400 HV0.3 | 250 – 350 HV0.3 |
Coating Application | Sliding Wear and Corrosion Resistance | Abrasion and Corrosion Resistance |
Finish Coating Thickness | 1 to 2mm | 1 to 2mm |