Infrastructure & Facility
The Plasmatron Advantage
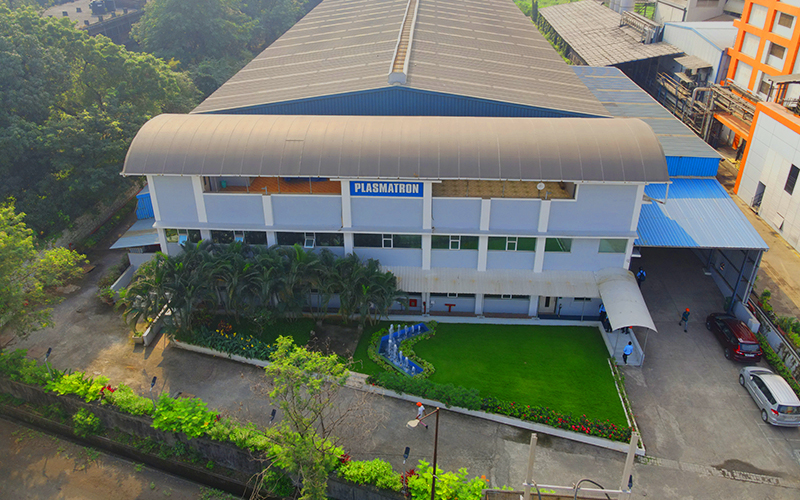
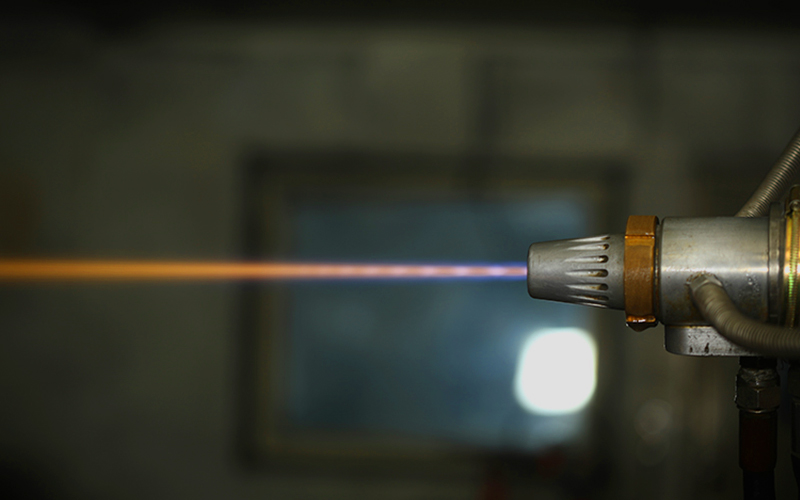
Coating
- Atmospheric Plasma Spray
- HP HVOF - Liquid Fuel
- Detonation Spray
- Wire Arc Spray
- Powder / Wire Flame Spray
- Spray & Fuse
Machining
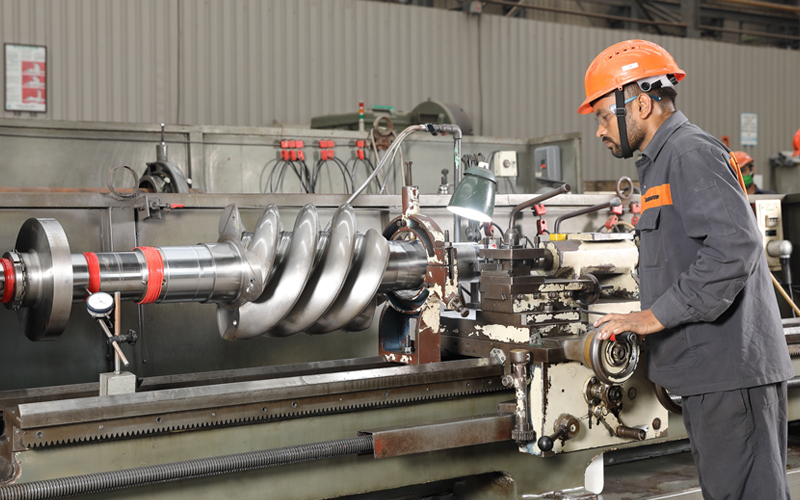
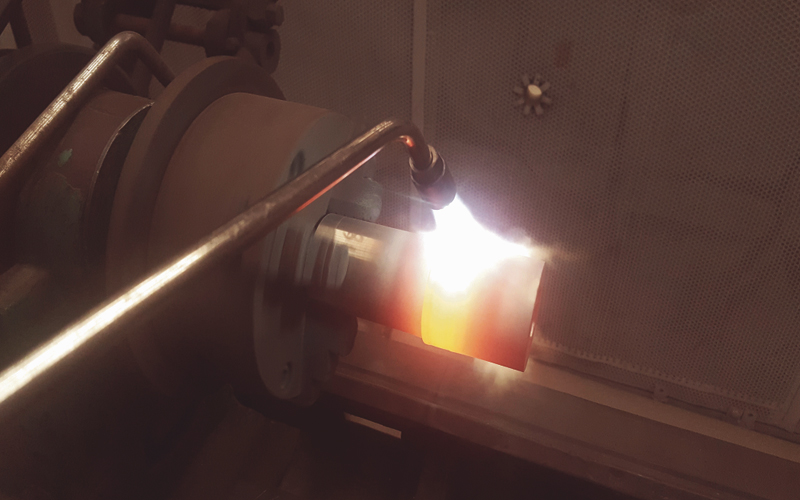
Cladding
Heat Treatment
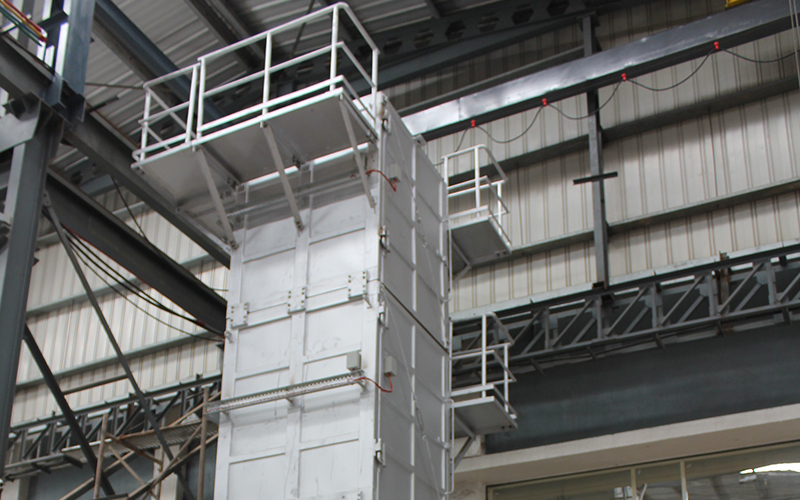

Super-finishing and Lapping
Coating R & D and Test Lab
Our extensive testing setup is an integral part of our quality system which enables us to monitor and improve our coating quality. We also have simulation test rigs to check the tribological behaviour of coatings like erosion, abrasion, fatigue and corrosion. We spray test coupons with every batch of the components to ensure consistent coating quality and instil customer confidence. Few of the tests that we conduct are :
- Micro-structure and Micro-hardness Evaluation (Thickness, Particle distribution etc.)
- Porosity Levels
- Coating Interface Bonding validation
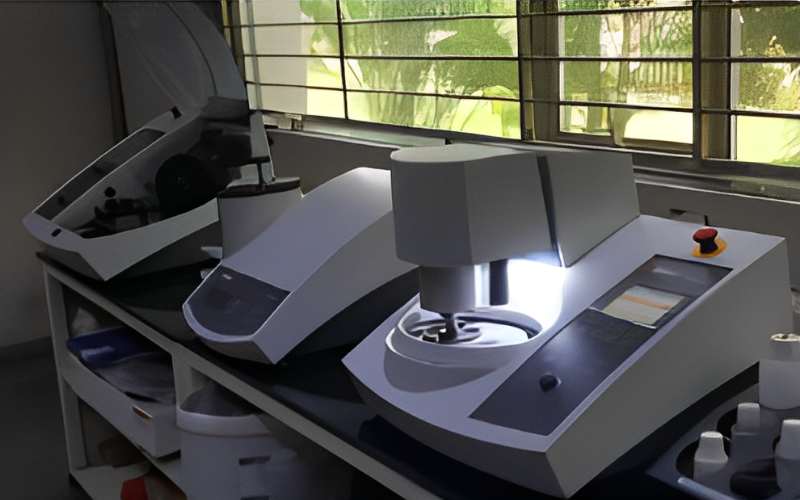
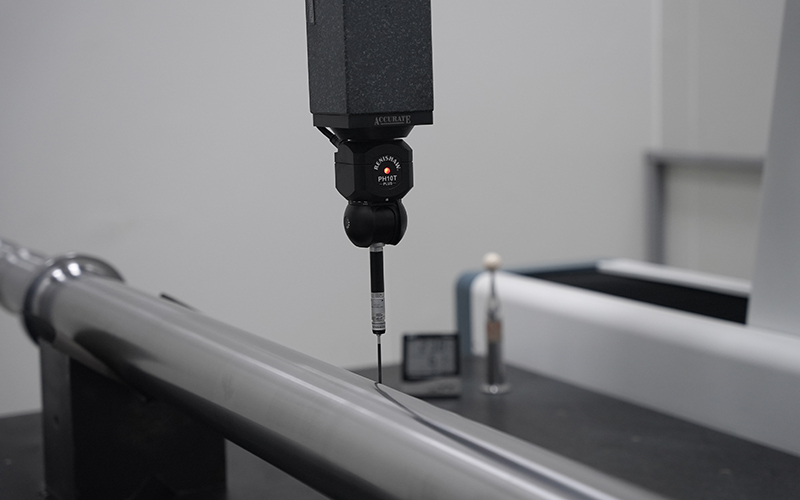
Inspection Facility
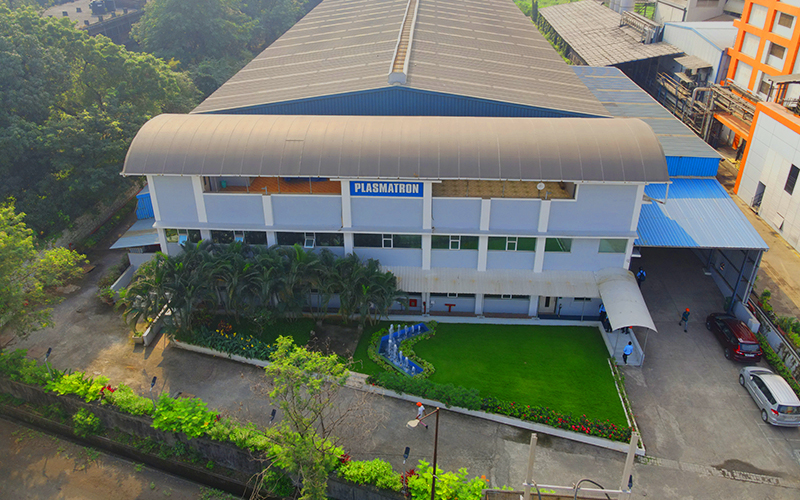
The Plasmatron Advantage
Plasmatron’s robust infrastructure enables it to cater to a wide variety of jobs ranging from large parts to smaller parts in larger volumes. We can do so with flexibility and while adhering to customer deadlines and quality requirements. With the complete spectrum of Thermal Spray coatings processes and a variety of pre & post coating machining setup under one roof, Plasmatron has established itself as a one-stop-shop for its esteemed clients. We have total working area of 35,000 sq. ft. and material handling capacity of 20 tons.
Coating
- Atmospheric Plasma Spray
- HP HVOF - Liquid Fuel
- Detonation Spray
- Wire Arc Spray
- Powder / Wire Flame Spray
- Spray & Fuse
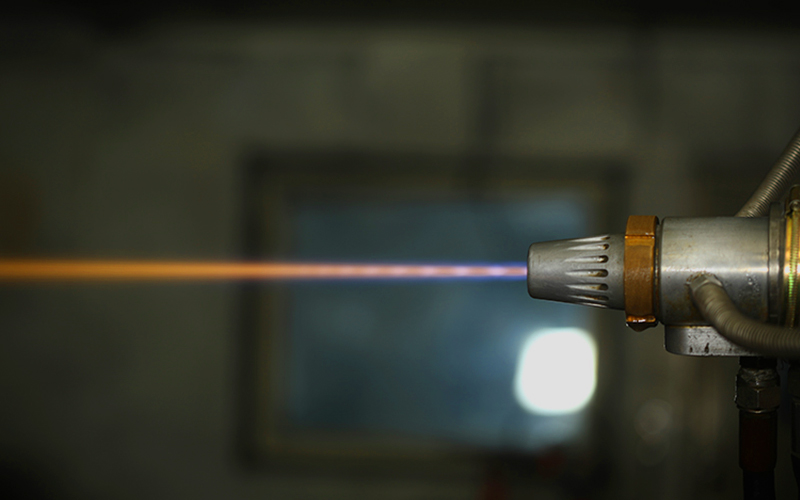
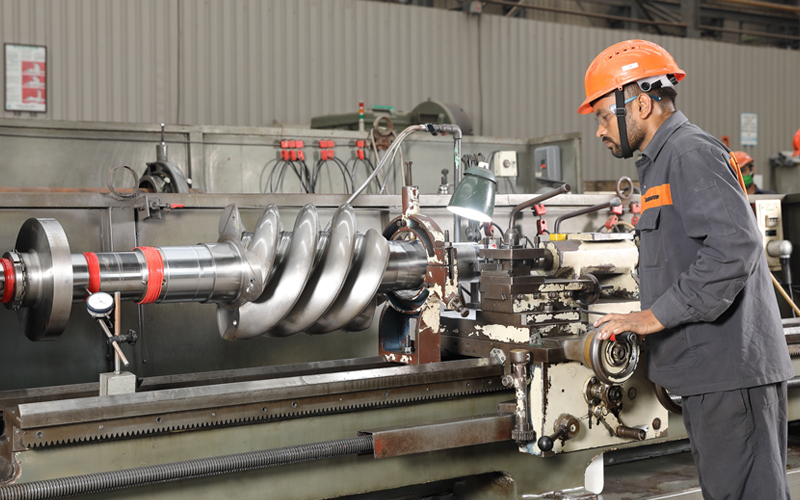
Machining
Plasmatron houses a wide range of machinery to carry out complete manufacturing of parts including pre-coating and post-coating machining operations. Our CNC VTL can handle cylindrical parts up to 2000mm diameter. Our other CNC Turning centers can handle diameters up to 900mm x Length 3000mm. Our grinding division has the capability of handling parts from diameter 10mm to 800mm. Our longest grinding setup can accommodate parts up to 6000mm length. We have a material handling capacity of upto 20 tons.
Cladding
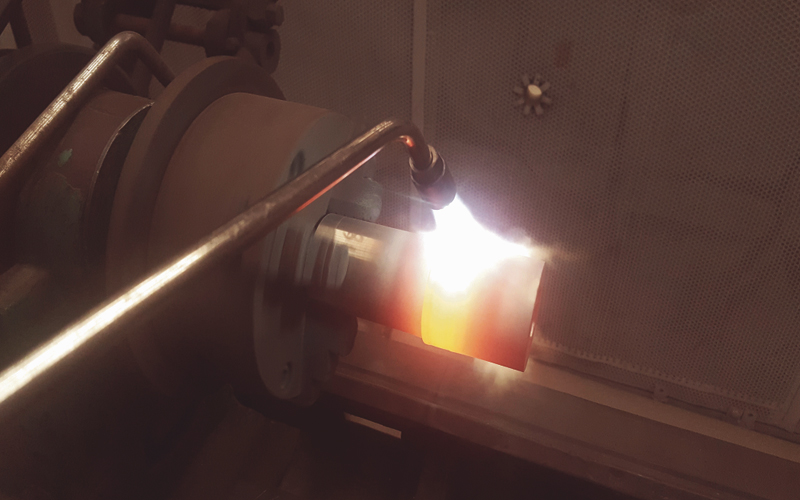
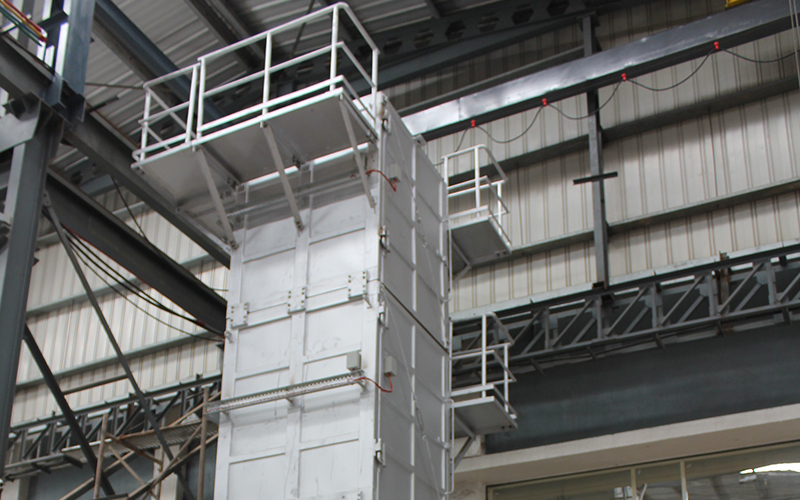
Heat Treatment
Super-finishing and Lapping

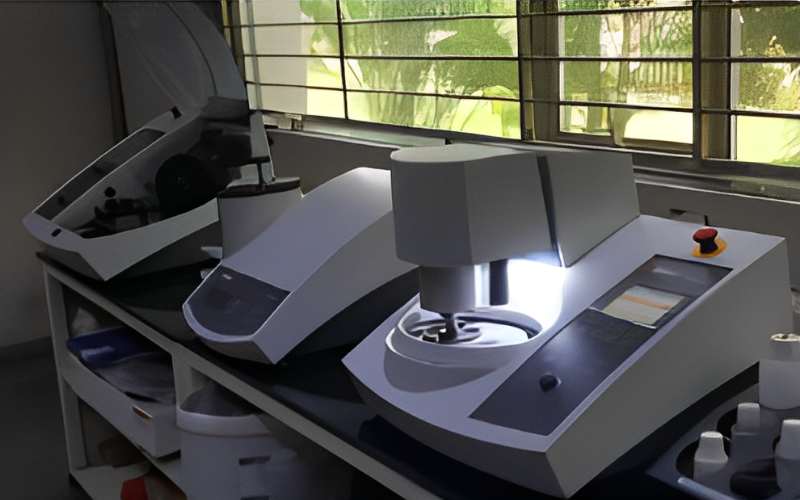
Coating R & D and Test Lab
Our extensive testing setup is an integral part of our quality system which enables us to monitor and improve our coating quality. We also have simulation test rigs to check the tribological behaviour of coatings like erosion, abrasion, fatigue and corrosion. We spray test coupons with every batch of the components to ensure consistent coating quality and instil customer confidence. Few of the tests that we conduct are :
- Micro-structure and Micro-hardness Evaluation (Thickness, Particle distribution etc.)
- Porosity Levels
- Coating Interface Bonding validation
Inspection Facility
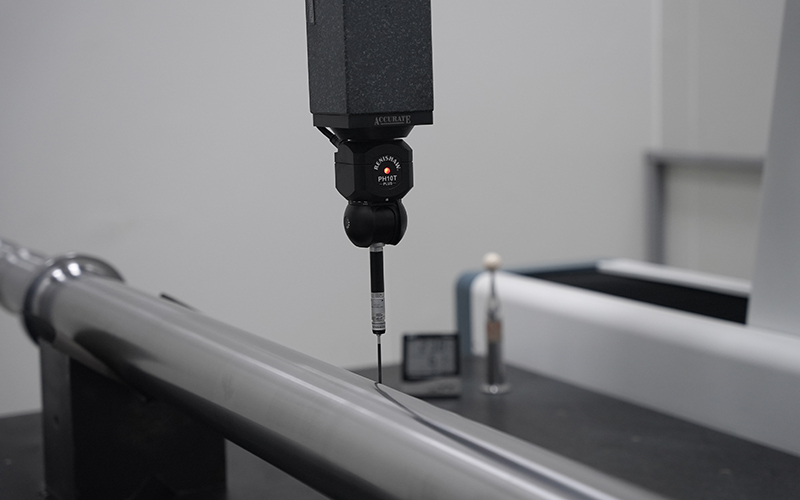