Hydraulic

Overview
Hydraulic cylinders employed for operation of dam gate, large valve, marine barge and dredger hulls are typically expected to last for 10 to 20 years based on its usage and location. Failure of these cylinders due to piston rod degradation and seal failure is a pre-dominant problem. Continuous exposure to corrosive environment and abrasive contaminants during functioning lead to premature wear and failure. Thermal sprayed ceramic and carbide coatings have gained wide popularity in the Hydraulic industry over the past few years owing to the tremendous benefits it offers over conventional surface treatment methods such as Nitriding and Hard chrome plating. Research have shown that the superior mechanical properties offered by HVOF sprayed coatings such as wear, abrasion and corrosion resistance coupled with low co-efficient of friction have demonstrated an increase in operational life and performance by 5 – 8x in comparison to Hard chrome plating.
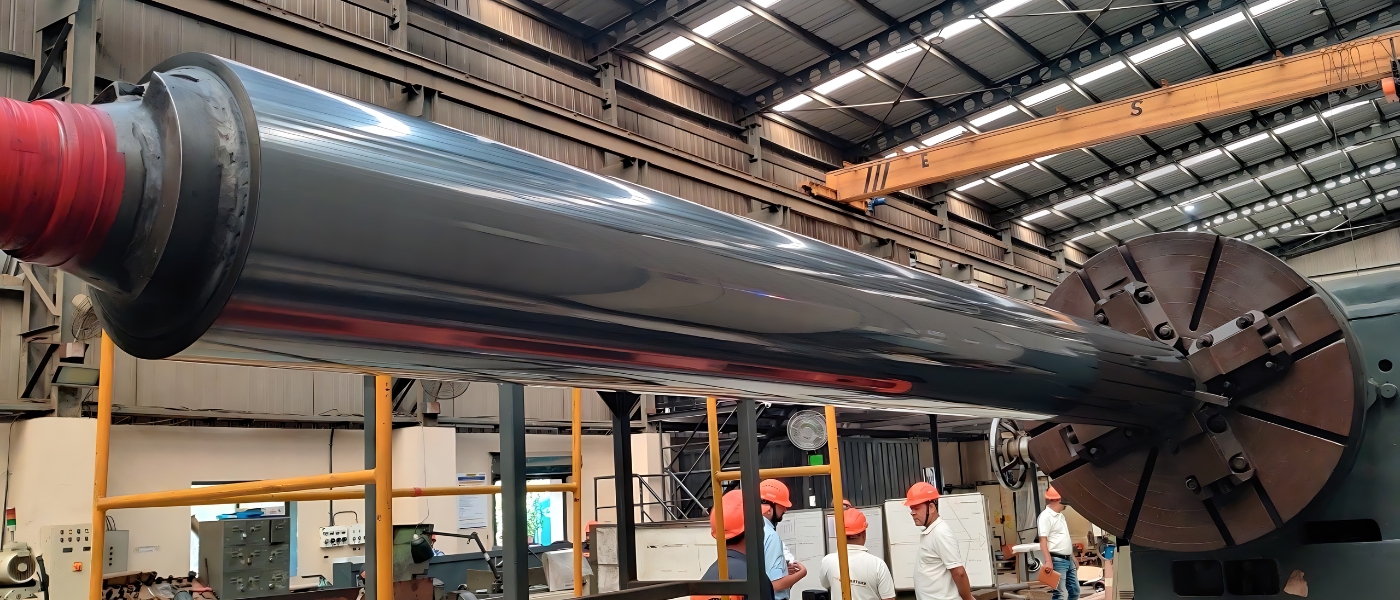
Problem
Hydraulic piston rods undergo reciprocating action on application of hydraulic pressure. They are utilized in a broad variety of industrial areas such as civil, industrial and offshore. During operation, hydraulic piston rods are exposed to a harsh and corrosive environment. Frequent operation and contaminants present in the operating environment lead to premature wear of the rod leading to failure of seals that would eventually deteriorate the functioning of the hydraulic system. Therefore smooth and hard surfaces are required on the outer diameter of the piston rod for proper sealing.
Thermal sprayed Hydraulic Piston rods are used in various industries such as :
- Mining
- Cranes
- Excavators
- Dams and Sluice doors
Solution
KERADEX B02
To combat this problem we offer KERADEX B02, which is an engineered ceramic coating with excellent wear and corrosion resistance properties ideal for Hydraulic piston rods. The ceramic layer is impervious and resistant to a wide range corrosive medium. KERADEX B02 coatings have been evaluated with Salt Spray test in accordance to DIN EN ISO 9227 for duration of 1500hrs. Precision finished KERADEX ceramic coatings ensure minimum friction with seal elements thereby enhancing operational life and performance. We have a complete in-house precision manufacturing and coating setup enabling us to meet high volume demands with consistent quality. We can manufacture and supply coated rods as per your specifications and MOC requirements. We have support for research and development to facilitate continuous improvement in quality and standard for coatings.
Coating Properties | KERADEX B02 |
---|---|
Micro Hardness | 900 – 1400 HV0.3 |
Porosity | < 5% |
Bond Strength | Up to 5000 Psi |
Finish Coating Thickness | 250 to 350 µm |
Surface Finish | < 0.4 Ra µm |