Gas Power
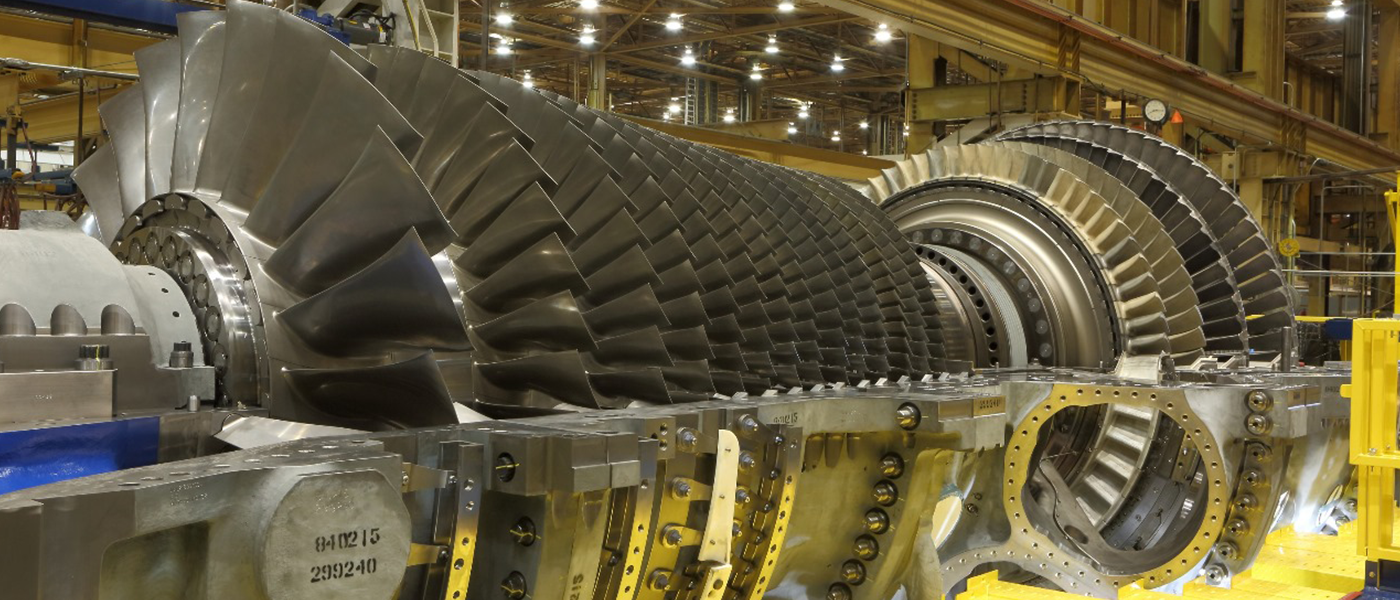
Gas Power
Problem
Gas turbine engines derive their power from burning fuel in a combustion chamber and using the high velocity combustion gases to drive a turbine in much the same way as the high pressure steam drives a steam turbine. One major difference however is that the gas turbine has a second turbine acting as an air compressor mounted on the same shaft. Gas turbines are generally considered the most cost effective and relatively environment-friendly large scale power generation technology, but their capacity as well as their thermal efficiency degrades under high ambient temperature conditions. In order to maintain the thermal efficiency atomized water is sprayed on the axial compressors. Nevertheless the water injection can cause droplet erosion on the first stages of blades of the compressor. Moreover interaction between mating gas turbine components due to vibrations can cause excessive wear and premature replacement. Oxidation at high operating temperature leads to the formation of oxides which is also a major reason for abrasive and corrosive wear and premature failure of components.
Solution
High Temperature Wear, Erosion and Corrosion Resistant Coatings
Components coming in contact with gas at high temperatures and subjected to impact loads and erosion can be coated with Chrome Carbide based Cermets like PIC DC12, PIC DC07 etc. and Nickel and Cobalt super-alloys like NiCrAlY and CoCrAlY. These coatings exhibit high temperature oxidation endurance and they prolong the operational life of critical components by enhancing wear and high temperature erosion resistant properties. Carbide coatings are deposited with robotic controlled HP-HVOF process to get uniform coating deposition and further impregnated with special sealant to achieve dense coating. Abradables are sprayed with Atmospheric Plasma Spray process for better clearance control & prevent gas leakage. Thermal barrier coatings are also sprayed on Turbine casings and Turbine blades by Atmospheric Plasma Process and sealed with special ceramic sealant to create an impervious barrier resistant to high temperature wear and oxidation. These coatings also help maintain the thermal efficiency of turbine and minimize heat loss.
Wear and Corrosion Resistant Coatings on Rotor Bearing Journals
We offer ceramic and carbide based coatings on rotor bearing journals to combat sliding wear and corrosion at high operating RPM’s. Our PIC B02 coating deposited with Atmospheric Plasma Spray process and impregnated with special sealer offer good resistance to abrasive and corrosive wear. Our PIC DC09 coating deposited with HP-HVOF process produces very dense and homogeneous coatings and offer excellent resistance to abrasive and sliding wear. These coatings are ground and super-finished to achieve the desired dimensions and surface finish. The coating and grinding process is carried out under controlled conditions and with necessary precautions to ensure that the run-out of journal areas is maintained within 0.01mm.
Coating Properties | PIC DC09 | PIC B02 |
---|---|---|
Process | HVOF | Plasma |
Bonding | Mechanical | Mechanical |
Micro Hardness (HRc) | 72 - 74 | 68 - 72 |
Coating Application | Abrasion and Sliding Wear Resistance | Abrasion and Corrosion Resistance |
Max Temperature (°C) | < 450 | < 540 |
Surface Finish | < 0.4 Ra µm |