Downhole Tools
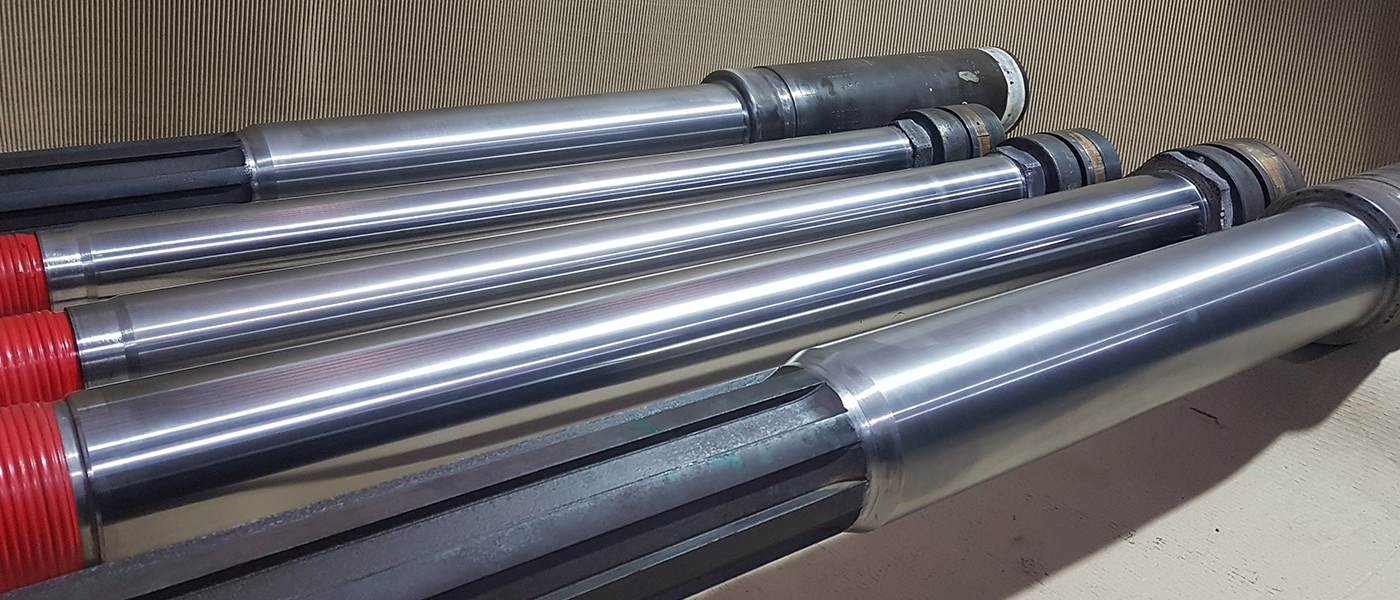
Downhole Tools
Problem
Down hole tools are an assembly of oilfield equipment that are used during well drilling and helps the oil well in optimizing the production levels and maintain continuous flow from a reservoir. These tools are subjected to heavy sliding wear and corrosion due to presence of abrasive slurry particles in the media. After certain period of operation the sealing surface of the tools wear out thereby increasing the clearance and reducing the operational efficiency. The drilling action is no longer effective and the entire assembly needs to be taken out to replace the worn out parts. The longevity of these tools is vital for improving productivity and reduce drilling cost. Chrome plating used to be the most commonly used coating for these components. Micro-cracks inherent to chrome plating weaken the mechanical properties of the plating, which leads to corrosion and degradation when the base metal is exposed to drilling muds, especially those with high chloride content. Additionally hard chrome plating is also an environmental hazard.
Solution
PIC DC Range of Coatings
Carbide Coatings has now become a permanent replacement for hazardous Hard Chrome Plating. Many research studies have been conducted and they have successfully proved that HP-HVOF sprayed carbide coatings are 8 – 10x more superior to Hard Chrome plating. Carbide coatings sprayed by HVOF process are consistent, dense, highly wear and corrosion resistant that ensures prolonged tool life and operational performance. Few advantages of HP-HVOF sprayed carbide coatings over Hard Chrome plating are as follows :
- HVOF Coatings more abrasive resistant than Hard Chrome plating
- Better fatigue strength to the component
- Provide better corrosion protection
- Wide range of coating material options are available in HVOF
- It is compatible with a vide range of substrates
We are globally qualified by renowned down hole tool equipment OEM’s for coating on new components as well as refurbishment of old worn out components. A list of tools which are coated and refurbished by us on a regular basis is as follows :
- Spline and Kelly Mandrel
- Neutralizer Mandrels
- Hydraulic Mandrels
- Knocker Mandrels
- Bearing Mandrels
- Sleeves
- Plungers
- Pony Rods
- Piston etc.
We have in-house setup for complete refurbishment of tools which were previously hard chrome plated or tungsten carbide coated. Tools which have excess wear are stripped to the base metal and metallized with PIC WC200 series material to restore original dimensions. The top layer is then coated with PIC DC09 to achieve desired wear and corrosion resistant properties followed by grinding and super finishing to achieve required size and surface finish.
We also carry out weld overlays on stabilizers and sleeves with our automated PTAW and GTAW process. This can be done for new as well as used parts.
Coating Properties | PIC DC07 | PIC DC09 | PIC DC12 |
---|---|---|---|
Micro Hardness (HV0.3) | 1100 - 1400 | 1100 - 1400 | 800 - 1100 |
Abrasion Resistance | Very Good | Excellent | Very Good |
Corrosion Resistance | Very Good | Very Good | Excellent |
Max Temperature | < 700°C | < 450°C | < 850°C |
Bond Strength | >10000 Psi | ||
Finish Coating Thickness | 150 to 250 µm (Excluding buffer layer for refurbished parts) | ||
Surface Finish | < 0.4 Ra µm |