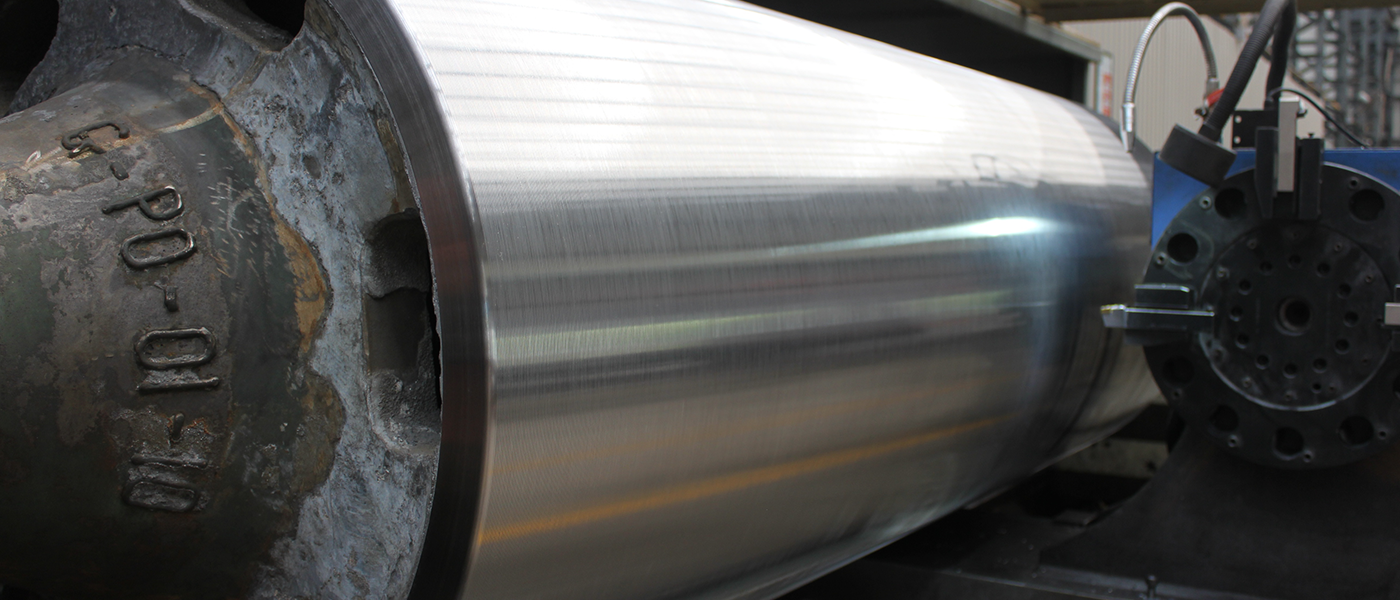
Continuous Galvanizing Line
GALDEX DB13 and PIC C59 Coating
We offer GALDEX DB13 coating on Sink and Stabilizer rolls, which is a dense and homogeneous coating that is non-reactive to molten Al and Zn. The coating is deposited through HP-HVOF process and sealed with an indigenously developed ceramic sealant. This prevents formation of dross over the barrel surface, thereby preventing damage to the galvanized sheet.
GALDEX DB13 restricts the diffusion of Zn and Al through the coating, which further enhances coating life and performance. The non-reactivity and anti-wetting properties of the coating prevent adhesion of zinc over the coated barrel surface thereby making it even easier for periodic cleaning and maintenance. GALDEX DB13 coated rolls have shown 5 – 8x better operational life without corrosive pitting on roll surface or dross formation in comparison to uncoated SS 316L rolls and 3 – 5x better operational life in comparison to conventional tungsten carbide coated rolls. We can supply complete coated sink and stabilizer rolls as per customer specification up to maximum diameter of 800mm. We also refurbish these rolls by stripping the damaged coating and machining micro grooves before coating which plays a vital role in its functionality. These micro grooves are machined to perfection on our heavy duty and calibrated CNC machines.
We have also indigenously developed PIC C59 coated Sink roll and Stabilizer roll sleeves to sustain the similar extreme operating conditions as encountered by Sink roll and Stabilizer rolls. These sleeves are completely manufactured in-house as per customer specification. The coating is deposited through Spray and Fuse process under controlled conditions. Each and every operation in the manufacturing of these sleeves is very critical right from machining of helical grooves to post-coating finishing of sleeves. Our PIC C59 coated sleeves have been successfully tested in operation and proven to increase the operational life by 3 – 5x as compared to conventional stellite coated sleeves. The metallurgic ally bonded coating also provides exceptional resistance to impact and abnormal vibrations.
Coating Properties | GALDEX DB13 | PIC C59 |
---|---|---|
Process | HVOF | Spray and Fuse |
Bonding | Mechanical | Metallurgical |
Micro Hardness | 700 – 900 HV0.3 | 850 – 1000 HV0.3 |
Coating Application | Molten Metal Abrasion and Corrosion Resistance | Molten Metal Abrasion Resistance |
Max Temperature | < 850°C | < 850°C |
Finish Coating Thickness | 150 to 180 µm | 0.8 to 1.5 mm |
Other Links
Plasmatron is a Reliable Surface Engineering Partner Providing Sink Rolls Coating services in Mumbai, Navi Mumbai, Thane, Agra, Ahmedabad, Ahmednagar, Ajmer, Amravati, Amritsar, Aurangabad, Bangalore, Beed, Belgaum, Bharuch, Bhavnagar, Bhopal, Bhubaneswar, Calicut, Chandigarh, Chandrapur, Chennai, Coimbatore, Cuttack, Daman, Delhi, Dhule, Ernakulam, Erode, Gangtok, Ghaziabad, Goa, Hubli, Hyderabad, Indore, Jaipur, Jalgaon, Jamshedpur, Jodhpur, Kolhapur, Kolkata, Lucknow, Ludhiana, Madurai, Mysore, Nagpur, Nashik, Noida, Patna, Pondicherry, Pune, Raipur, Rajkot, Salem, Satara, Secunderabad, Shimla, Sikkim, Silvassa, Solapur, Srinagar, Surat, Udaipur, Vadodara, Valsad, Vellore, Vijayawada, Visakhapatnam, India