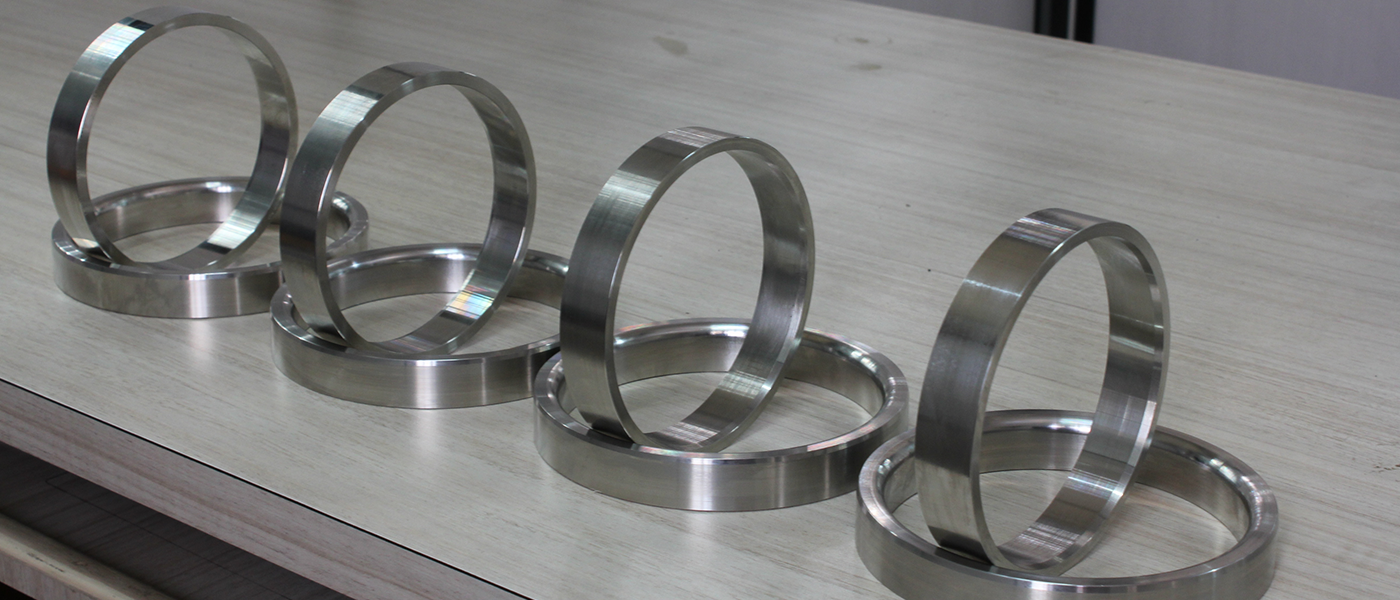
Casing and Impeller Wear Rings
Problem
Impeller and casing wear rings are subjected to two different forms of wear. Even in the absence of any solid particles in the process fluid, the wear rings can be damaged by sliding wear (also called metal-to-metal wear) due to unintentional contact between the rotating (e.g. impeller wear ring) and stationary (e.g. casing wear ring) surfaces resulting in wear ring rub.
This is especially problematic with most corrosion resistant alloys which have a propensity for metal-to-metal wear and/or galling, and the severe seizure of a pump fitted with austenitic stainless steel wear rings.
To reduce the risk of seizure it is prudent to use dissimilar metals for casing and impeller wear rings, ensure a minimum 50HB hardness difference between the rings or coat the wearing surfaces with a suitable anti-galling coating.
If there are any solid particles present in the process medium the particles can move through the wear ring interface if they are small enough, due to the pressure differential across the wear ring, and depending on the size of the particle this can result in abrasion (e.g. when particles are approximately the same size as wear ring clearance) or erosion (e.g. when particles are much smaller than wear ring clearance).
Solution
Wear and Corrosion Resistant Coatings
Our tungsten carbide based coatings provide excellent abrasion and corrosion resistance against harsh fluids flowing through the casing and wear rings. These coatings can be applied with HP-HVOF process that produces a dense and homogeneous coating through repeated and controlled deposition. The cross section of ring being very thin, necessary precautions are taken during the coating process to ensure that the temperature is controlled and rings are not distorted. The coatings are ground and polished using customized fixtures with at most precision to achieve desired size and surface finish. Certain applications demand deposition of nickel based materials such as Colmonoy by Spray and Fuse method whereas others demand deposition of cobalt based material through PTAW process.
We can provide complete coated and cladded wear and casing rings as per customer requirement. We have in-house setup to manufacture rings of various sizes and meet high volume demands.
Coating Properties | PIC C53 | PIC C832 | PIC DC09 | PIC B02 |
---|---|---|---|---|
Process | PTAW | Spray and Fuse | HVOF | Plasma |
Bonding | Metallurgical | Metallurgical | Mechanical | Mechanical |
Micro Hardness (HRc) | 42 - 48 | 58 - 64 | 72 - 74 | 68 - 72 |
Coating Application | Erosion and Corrosion Resistance | Abrasion Resistance | Abrasion and Corrosion Resistance | Abrasion and Corrosion Resistance |
Surface Finish | < 0.4 Ra µm |