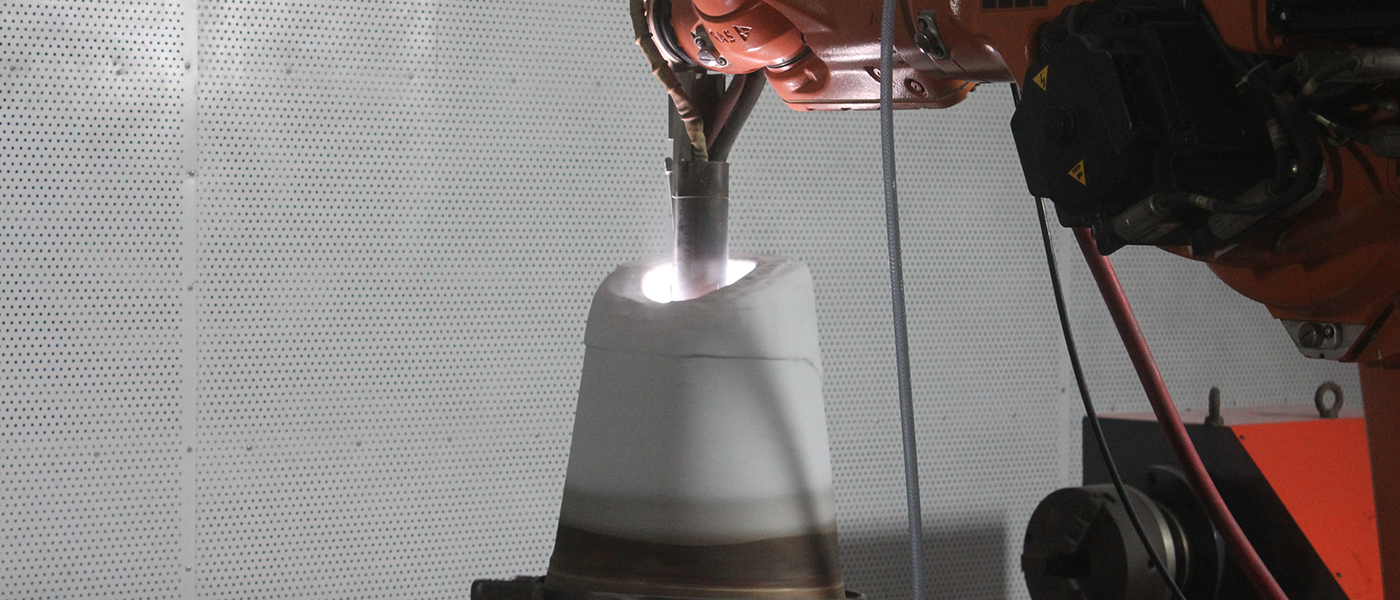
Blast Furnace Copper Tuyeres
Problem
Copper Tuyeres used for injecting pulverized coal into the Blast Furnace are subjected to extreme temperatures and they undergo heavy wear from abrasion from slag and molten iron. Failure in tuyeres mostly occurs due to overheating and puncturing of the copper casting. Once a tuyere fails it can only be replaced by shutting the entire blast furnace which translates to heavy downtime and Production losses. Also the occurrence of failure is random and not dependent on the time the tuyere has been in operation. This makes it even more unreliable and significantly adds to the contingent maintenance and operational expenses.
Solution
KERADEX D11 Coating for Copper Tuyeres
KERADEX D11 is a dense ceramic composite developed for high temperature abrasion and erosion resistance. The coating is capable of withstanding thermal shocks without cracking or spallation. KERADEX D11 is a novel solution for tuyeres wherein it not only imparts high temperature wear resistance but also shields the tuyere in form of a thermal barrier. The coating gradient helps in absorbing thermal shocks without spallation and the ceramic densified outer layer imparts outstanding wear and erosion resistance at high temperatures. KERADEX D11 applied on copper tuyeres significantly improves its operational life thereby reducing unexpected downtime costs and production loss. Based on the end application the formulation of the coating could be further tweaked to achieve best performance.
We have supplied KERADEX D11 coated tuyeres to renowned OEM’s and End users in INDIA. Our KERADEX D11 coated copper tuyeres have been successful in operation and exhibited operational life of 3 – 4x as compared to conventional ceramic coated tuyeres.
Coating Properties | KERADEX D11 |
---|---|
Hardness Gradient | 380 - 1000 HV0.3 |
Coating Application | High Temperature Abrasion and Erosion Resistance |
Max Temperature | < 900°C |
Finish Coating Thickness | 800 to 1200 µm |
Plasmatron is a Reliable Surface Engineering Partner Providing Furnace Copper Tuyeres Coating services in Mumbai, Navi Mumbai, Thane, Agra, Ahmedabad, Ahmednagar, Ajmer, Amravati, Amritsar, Aurangabad, Bangalore, Beed, Belgaum, Bharuch, Bhavnagar, Bhopal, Bhubaneswar, Calicut, Chandigarh, Chandrapur, Chennai, Coimbatore, Cuttack, Daman, Delhi, Dhule, Ernakulam, Erode, Gangtok, Ghaziabad, Goa, Hubli, Hyderabad, Indore, Jaipur, Jalgaon, Jamshedpur, Jodhpur, Kolhapur, Kolkata, Lucknow, Ludhiana, Madurai, Mysore, Nagpur, Nashik, Noida, Patna, Pondicherry, Pune, Raipur, Rajkot, Salem, Satara, Secunderabad, Shimla, Sikkim, Silvassa, Solapur, Srinagar, Surat, Udaipur, Vadodara, Valsad, Vellore, Vijayawada, Visakhapatnam, India