Aerospace
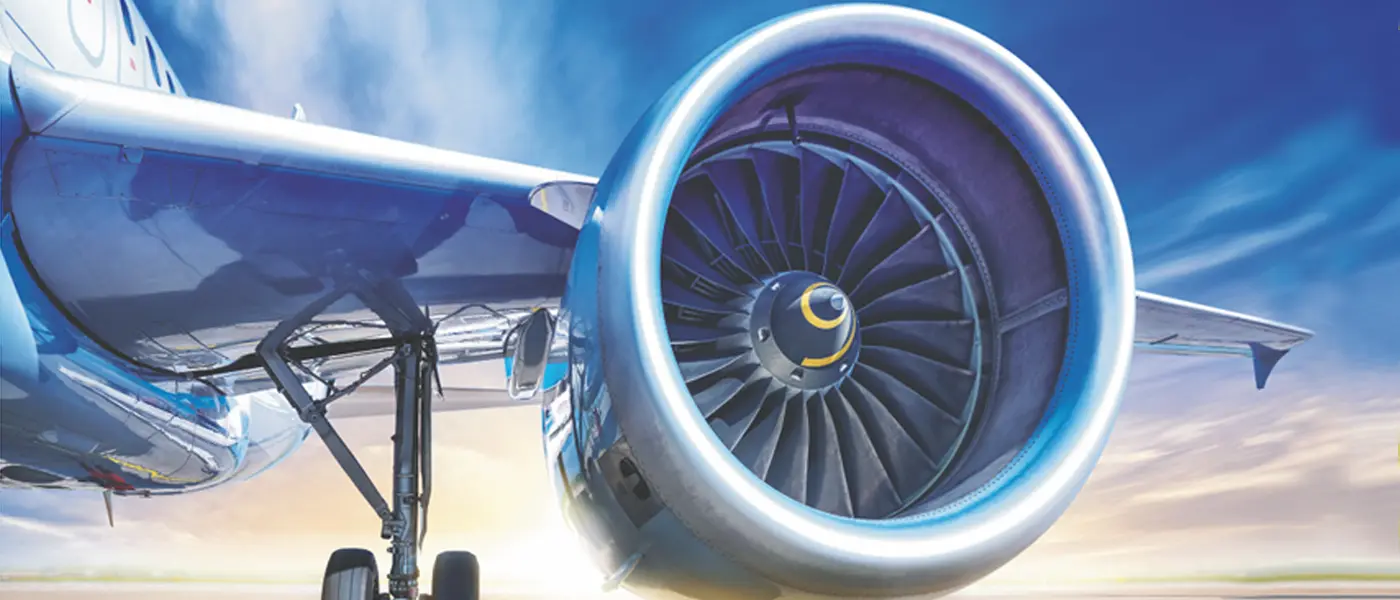
Overview
Aerospace is one of the largest and most promising industry sectors demanding rapid technological advancement owing to its sophisticated operating functions. This naturally instill the need of thermal spray coating in many applications ranging from Airframe and propulsion systems to Landing gears which require high performance and quality requirements. Different type of coatings including Ceramic, Metal, Cermet and Composites are sprayed on different components which are subjected to harsh operating environment. These coatings not only increase the durability but also the reliability due to its inherent characteristic to sustain extreme operating conditions. In the Aerospace domain, Safety is not an option but an obligation which is communicated and mandated to all stakeholders throughout the supply chain. The Aerospace market has witnessed tremendous growth over the past few decades due to increasing demand and beholds great opportunities in the future.
Problem
The Aerospace industry is one of the first industries that have completely accepted Thermal spray coatings. An aircraft engine is a component of the propulsion system for an aircraft that generates mechanical power. Aircraft engines are almost always either lightweight piston engines or gas turbines. A variety of degradation problems exist in aircraft engines as a result of metal to metal wear, fretting, hot corrosion, particle erosion etc. This degradation is accelerated due to the high temperature conditions involved. Thermal sprayed coatings impart the required surface condition to increase the life of certain engine components. There are more than hundred critical components inside an aircraft engine which are coated. Without the use of these thermal sprayed coatings a turbine will not operate at optimum levels. Performance guarantee of coatings in the Aviation industry is at most important. Any failure in coating may lead to major mishap.
Solution
High Temperature Wear, Corrosion and Oxidation Resistant Coatings
We can provide a range of ceramic, carbide and cermet based coatings for various parts operating at different sections in an aircraft engine. The coating material and grade selection is primarily done by the OEM. However the control of coating process and the implementation of Quality Management System is what matters in execution of coatings for Aerospace parts. We have successfully adopted and implemented AS 9100 Rev D. Quality Management System and continuously undergoing process qualifications from different OEM’s. The principles of PDCA and Risk Management are imbibed deep in our day to day functioning. Our HVOF and Plasma control systems are completely automated and programmed with necessary safety interlocks to ensure that neither the process nor the customer component shall be hampered. We also have an in-house sophisticated machine shop to cater to all manufacturing requirements of Aero engine parts.
Coating applications in Aircraft engine parts have been standard for a long while. The Aircraft engine can primarily divided into three section based on their operation :
- Combustion Section
- Turbine Section
- Compressor Section
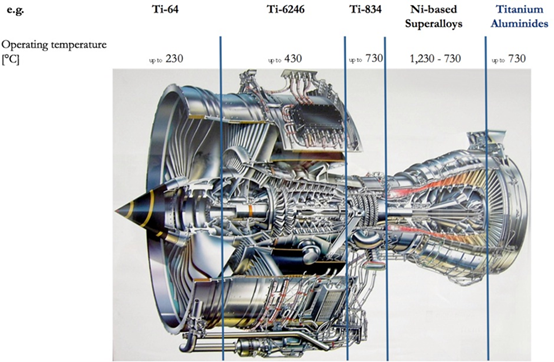
Below is a list of parts that are coated to sustain varying operating conditions :
Combustion Section | ||
---|---|---|
Part Name | Coating Type | Coating Objective |
Combustion Chamber Liners and Domes | Thermal Barrier | Thermal Barrier |
Combustion Chamber Cases | Al-Ceramic | Corrosion Resistance |
Combustion Chamber Clamp and Liner | Chrome Carbide | Fretting Wear Resistance |
Combustion Chamber Positioning Pin | Tungsten Carbide and Chrome Carbide | Fretting Wear Resistance |
Combustion Chamber Support Assembly | Chrome Carbide | Fretting Wear Resistance |
Fuel Nozzle Nut and Swirler | Chrome Carbide | Fretting Wear Resistance |
Turbine Section | ||
---|---|---|
Part Name | Coating Type | Coating Objective |
Air Sealing Rings | Chrome Carbide | Fretting Wear Resistance |
Exhaust Pins and Bushings | Tungsten Carbide | Fretting Wear Resistance |
Outer Air seals and Turbine Shrouds | Thermal Barrier | Thermal Barrier with Erosion Resistance |
Turbine Blades | LCO-17, Tungsten Carbide | Rubbing and Fretting Wear Resistance |
Turbine Blade Tips | Abradables | Sealing at tip of turbine blade |
Turbine Blades and Vanes | Thermal Barrier | Thermal Barrier |
Turbine brush Seals | Chrome Carbide | Sliding Wear Resistance |
Turbine Stator Shrouds | Chrome Carbide | Fretting Wear Resistance |
Compressor Section | ||
---|---|---|
Part Name | Coating Type | Coating Objective |
Bevel Gear and Gearbox Drive | Tungsten Carbide | Fretting Wear Resistance |
Bleed Manifold Expansion Joint Liners and Sleeves | Tungsten Carbide | Fretting Wear Resistance |
Compressor Blades | Alumina Titania, Tungsten Carbide and Chrome Carbide | Wear Resistance, Solid particle Erosion Resistance |
Compressor Vanes and Stators | Al-Ceramic | Corrosion Resistance |
Compressor Case | AL-Ceramic, Tungsten Carbide | Corrosion and Oxidation Resistance, Fretting Wear Resistance |
Compressor Hubs and Disks | Tungsten Carbide | Fretting Wear Resistance |
Turbine brush Seals | Chrome Carbide | Sliding Wear Resistance |
Compressor Rotor Tubes and Sleeves | Tungsten Carbide | Fretting Wear Resistance |
Diffusers, Impellers and Vane Sectors | Tungsten Carbide | Erosion Resistance |
Bearing & Other Accessories | ||
---|---|---|
Part Name | Coating Type | Coating Objective |
Bearing Housings and Seal Assemblies | Tungsten Carbide and Chrome Carbide | Sliding Wear Resistance |
Bearing Seal Housings | Tungsten Carbide | Fretting Wear Resistance |
Bearing Seal Seats and Spacers | Tungsten Carbide and Chrome Carbide | Sliding Wear Resistance |
Labyrinth Seal Fins | Tungsten Carbide and Chrome Carbide | Sliding Wear Resistance |
Oil Pump Gears and Breather Tubes | Tungsten Carbide | Fretting Wear Resistance |