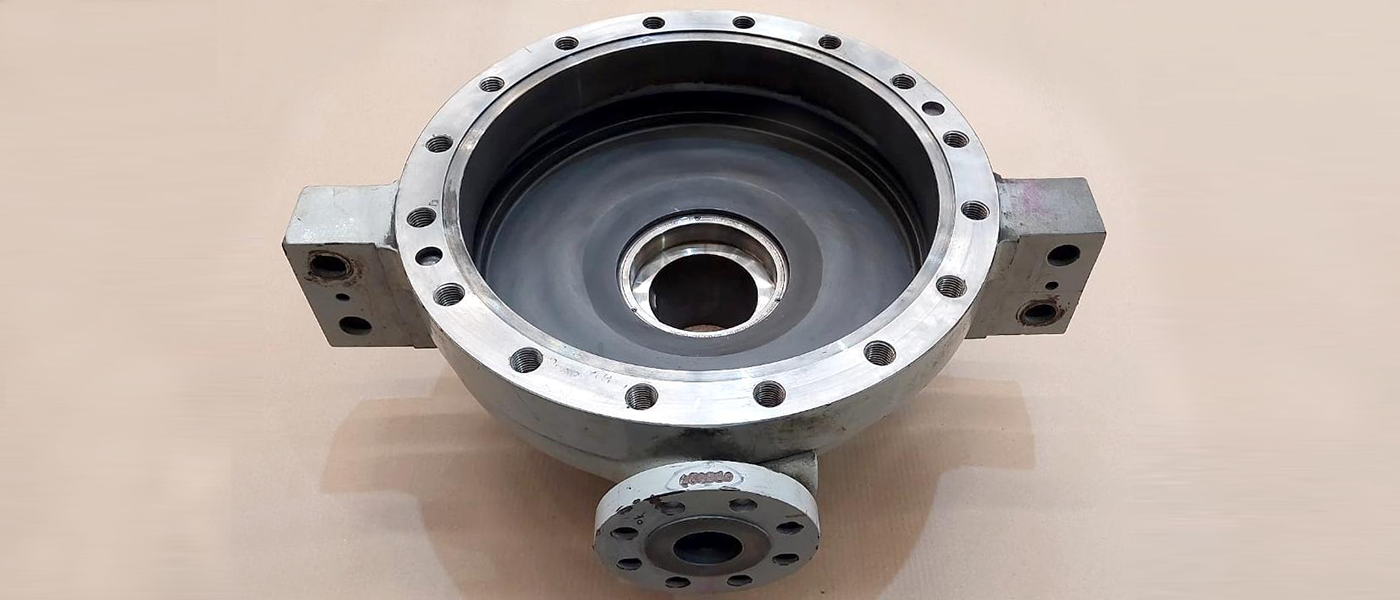
Centrifugal Pump Parts
Problem
An impeller is a rotating component of a centrifugal pump which transfers energy from the motor that drives the pump to the fluid being pumped by accelerating the fluid outwards from the center of rotation. In critical applications the media flowing through pumps carry abrasive and erosive substances such as sand or silt. These substances move through all the fluid channels, impeller sidewalls and close clearances inside the pump. If the size of abrasive particles is less than the clearance, they move freely and impact the casing at shallow angle causing erosive wear. If the particle size is same as the clearance, it may clog between the impeller and casing thereby causing three body abrasions. Under severe operating conditions the effect of abrasion, corrosion and cavitation may lead to accelerated wear rate leading to unexpected breakdown and heavy maintenance costs.
Solution
PIC DC Range of Coatings
We provide a range of tungsten carbide based coatings which are impermeable and sustain the effect of abrasive, erosive and corrosive particles flowing through pumps. Our range of coatings can be applied with HP-HVOF process that produces a dense and homogeneous coating and used in wear and corrosion resistant applications. The coatings are ground and polished to achieve the desired tolerances and surface finish. Our coatings can be applied on impeller guide vanes, impeller shaft bearing journals and pump casings. Our coated pump parts have been operating successfully over the years for applications in Oil and Gas, Power plants, slurry pumping etc.
Industry | PIC DC07 | PIC DC09 | PIC DC12 |
---|---|---|---|
Micro Hardness (HV0.3) | 1100 - 1400 | 1100 - 1400 | 800 - 1100 |
Coating Application | Erosion and Corrosion Resistance | Abrasion and Corrosion Resistance | High Temperature Corrosion Resistance |
Max Temperature (°C) | < 700 | < 450 | < 850 |
Bond Strength | >10000 Psi | ||
Finish Coating Thickness | 150 to 250 µm | ||
Surface Finish | < 0.8 Ra µm |